Efficient dosing processes: Control vs. regulation - what makes the difference?
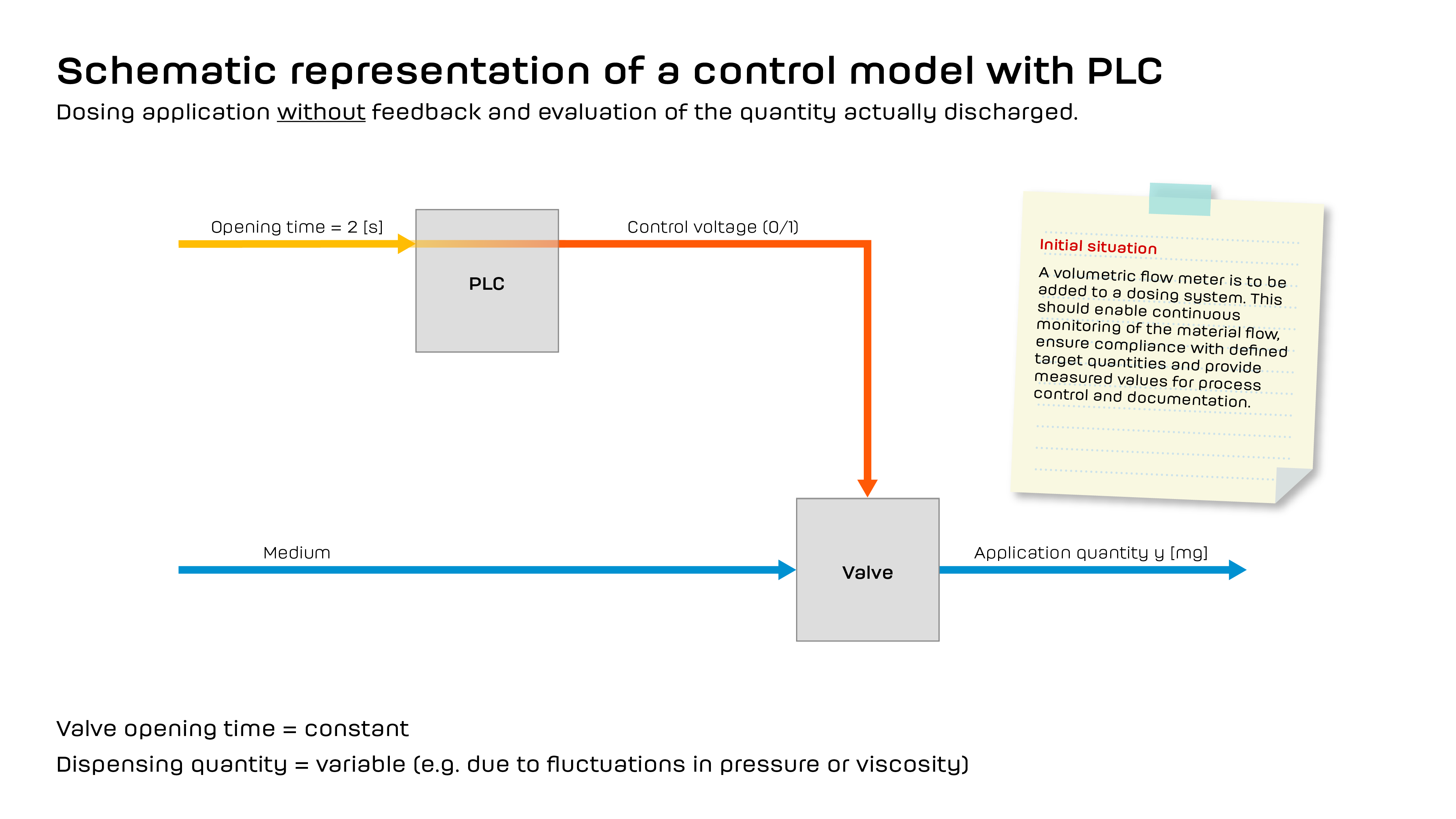
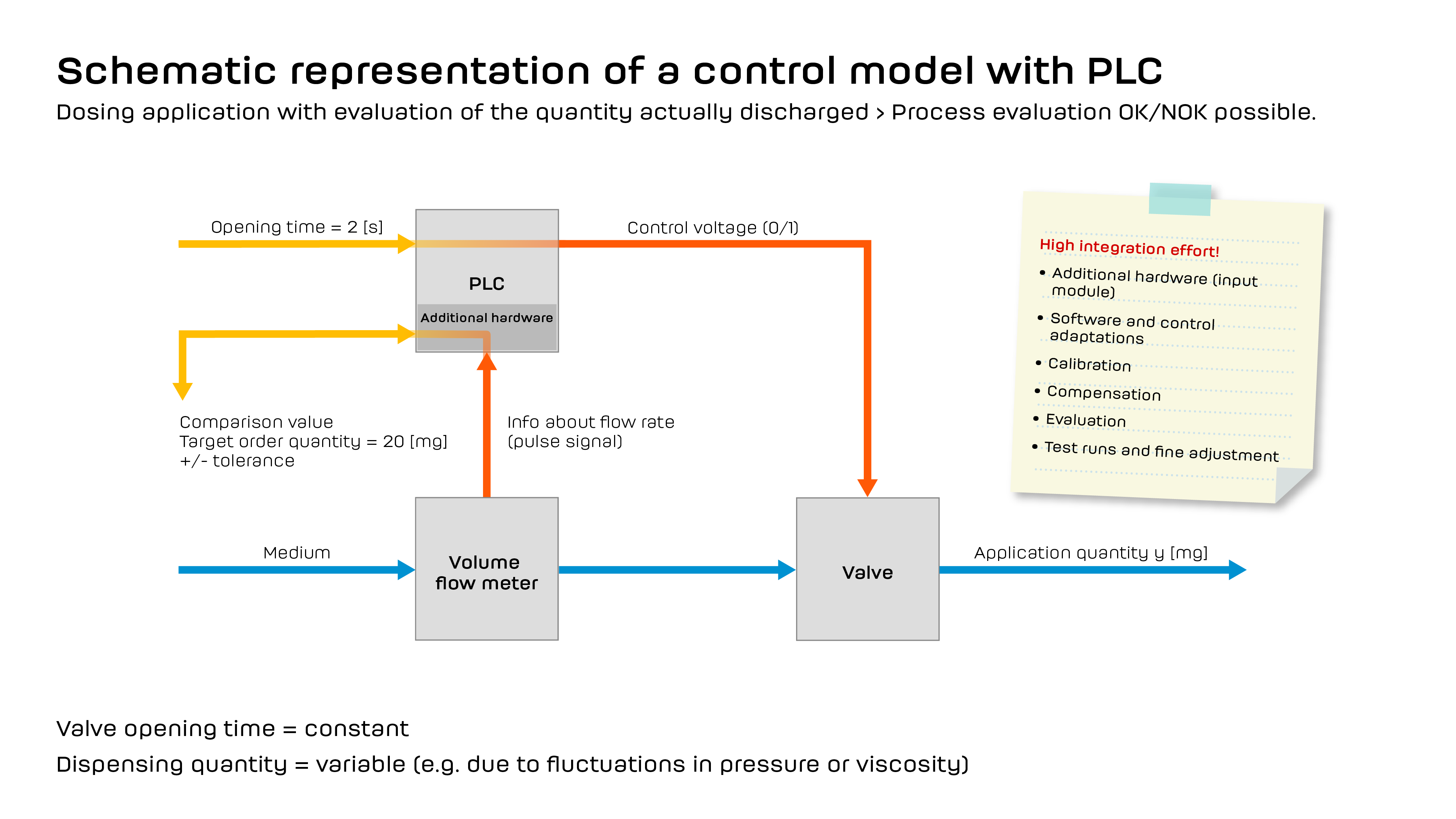
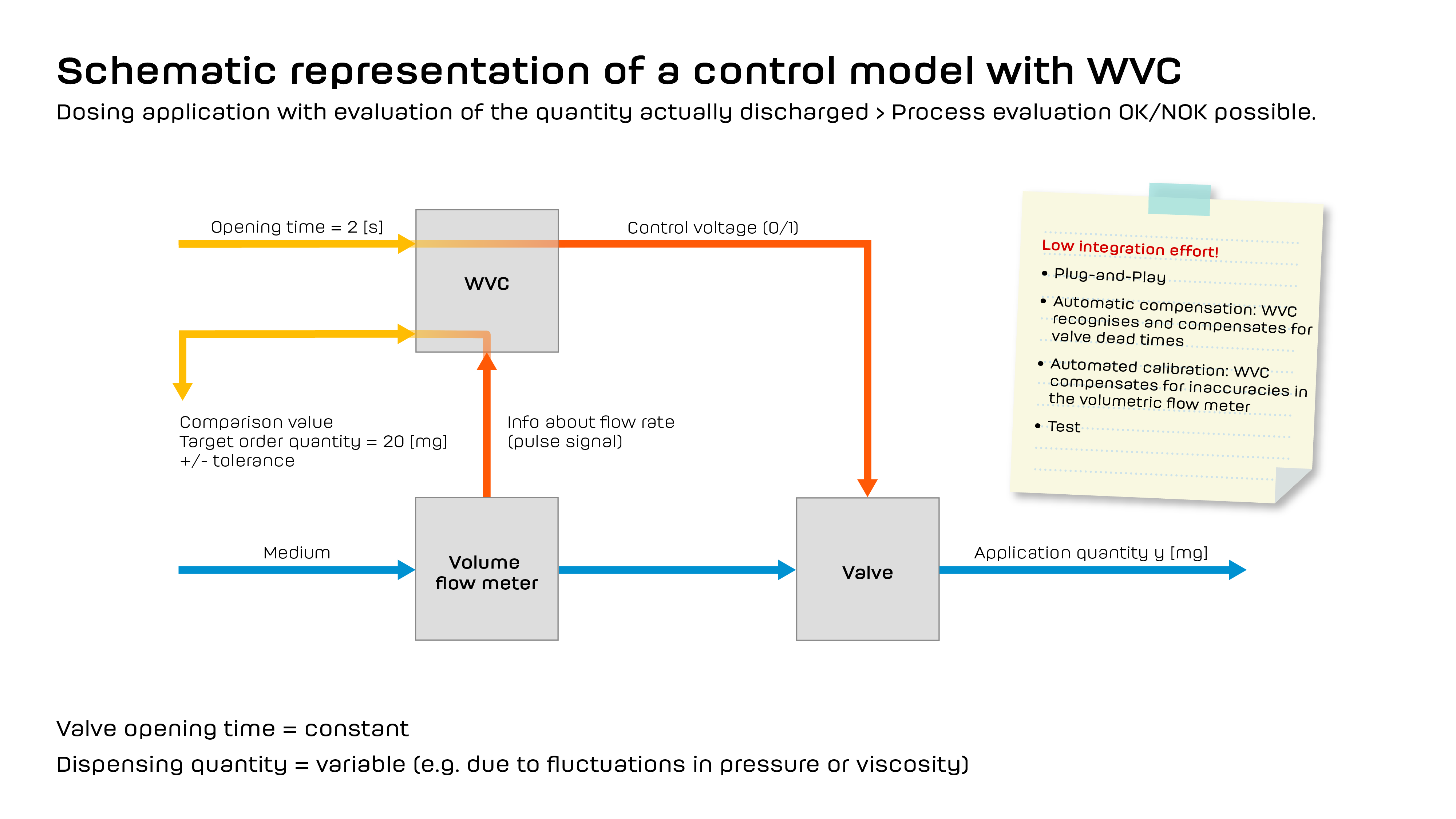
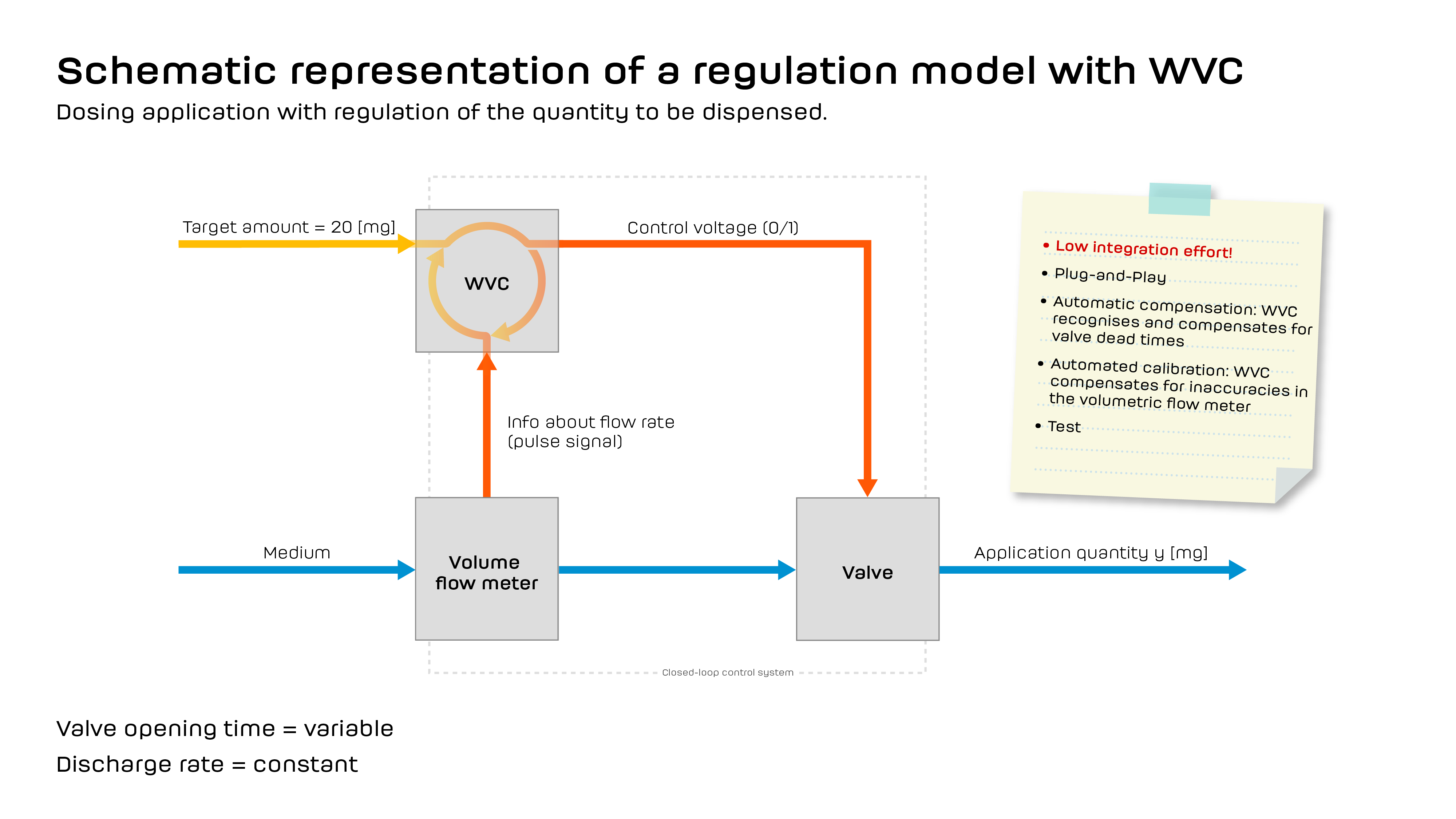
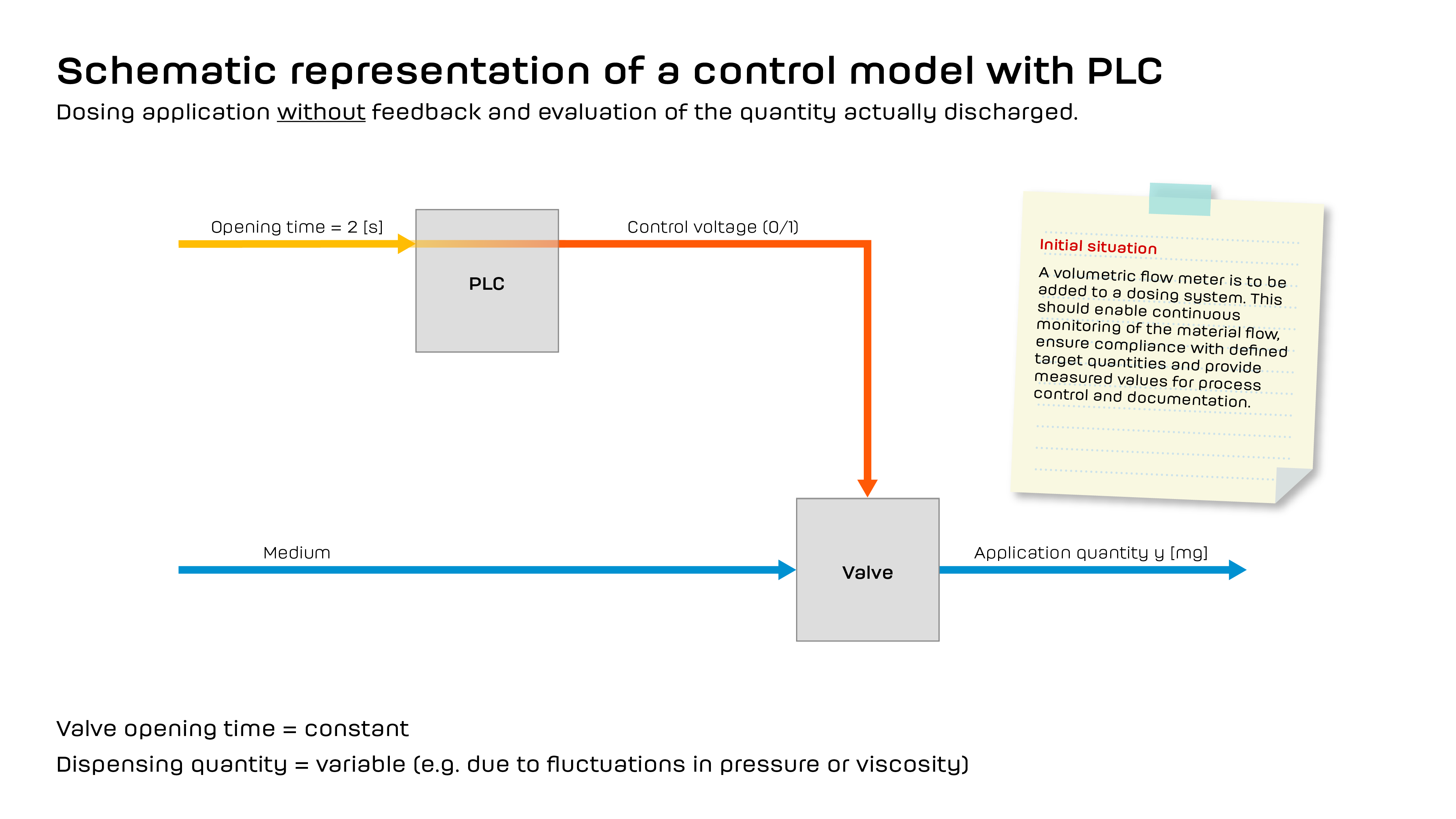
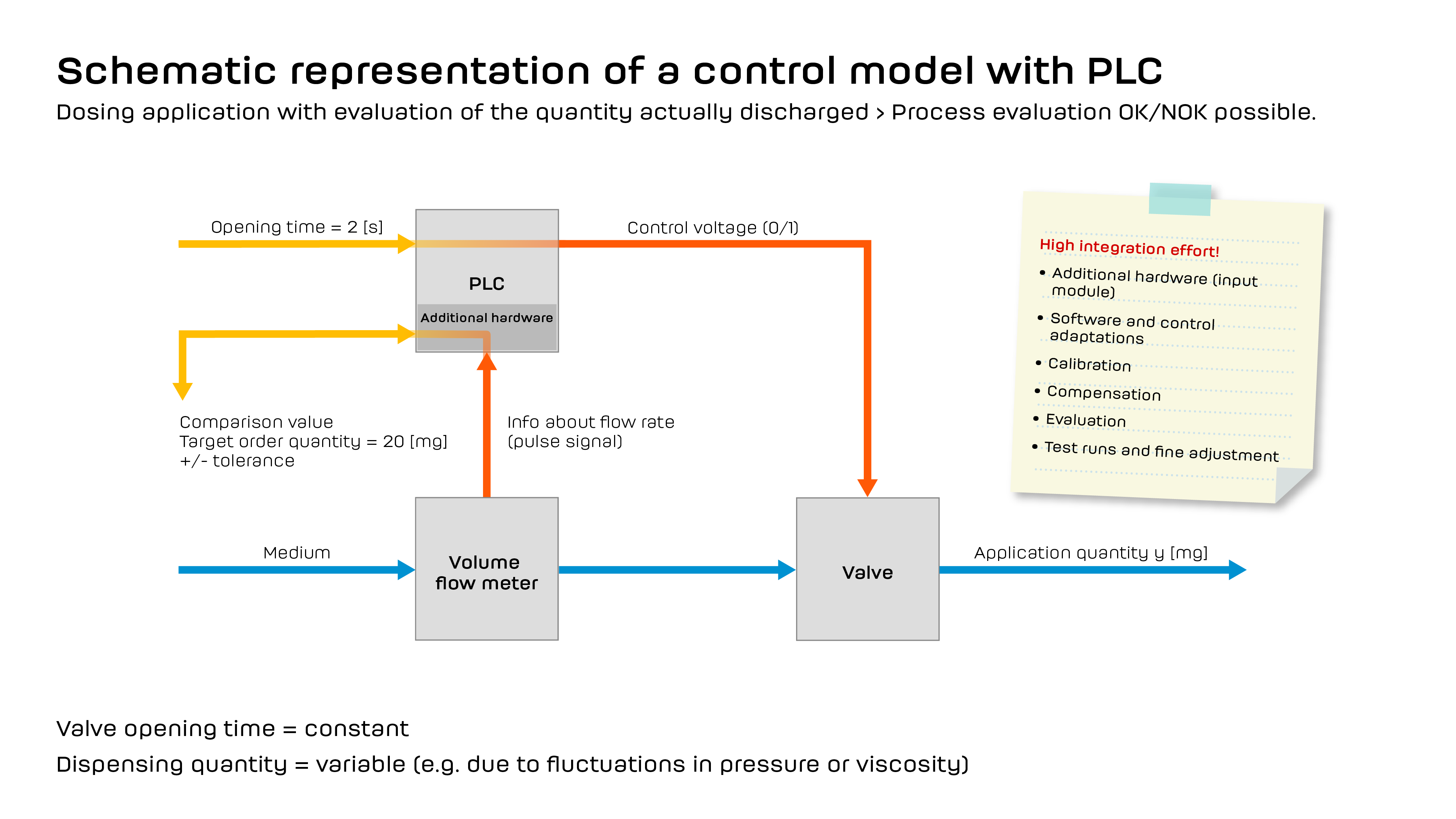
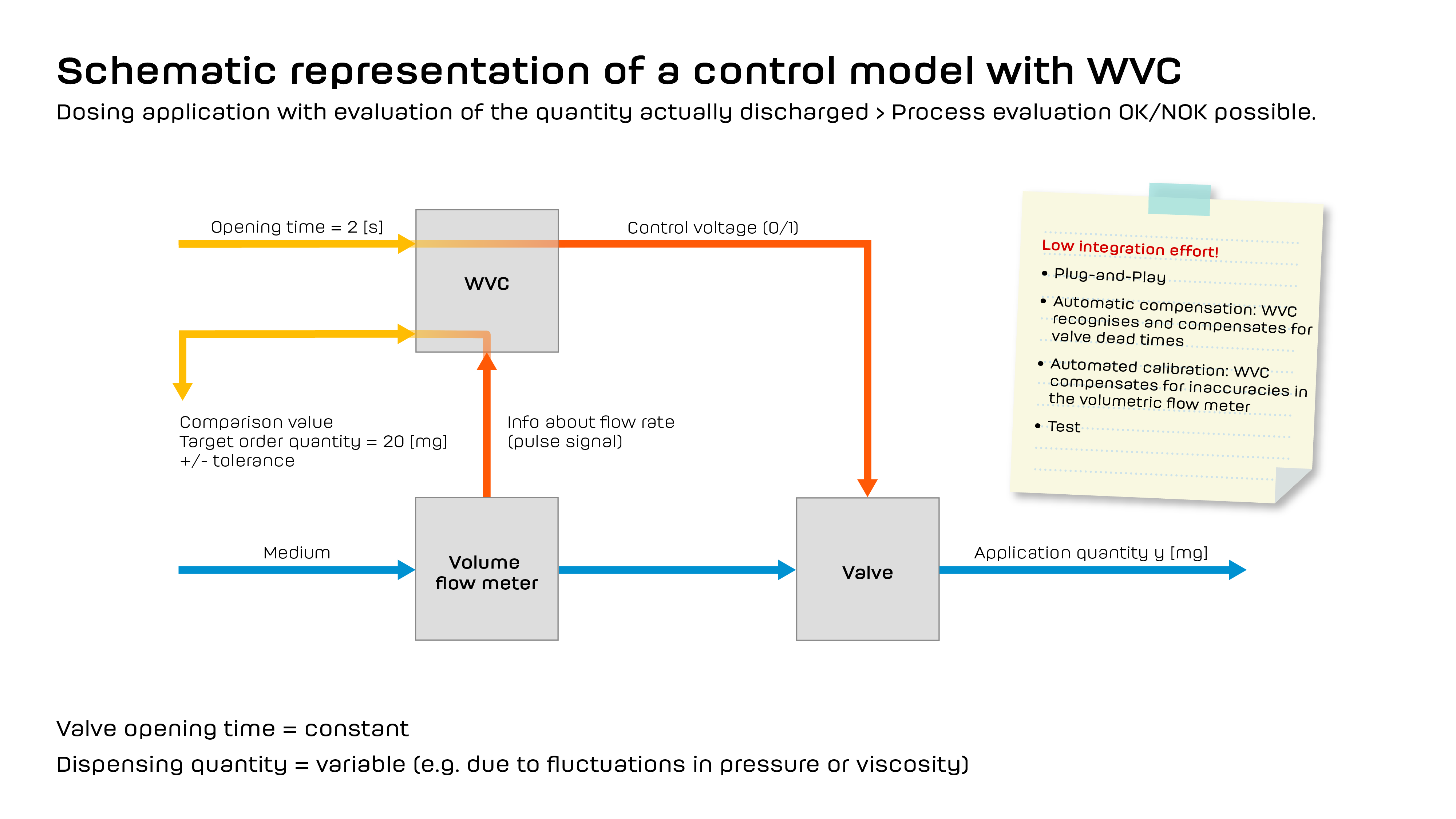
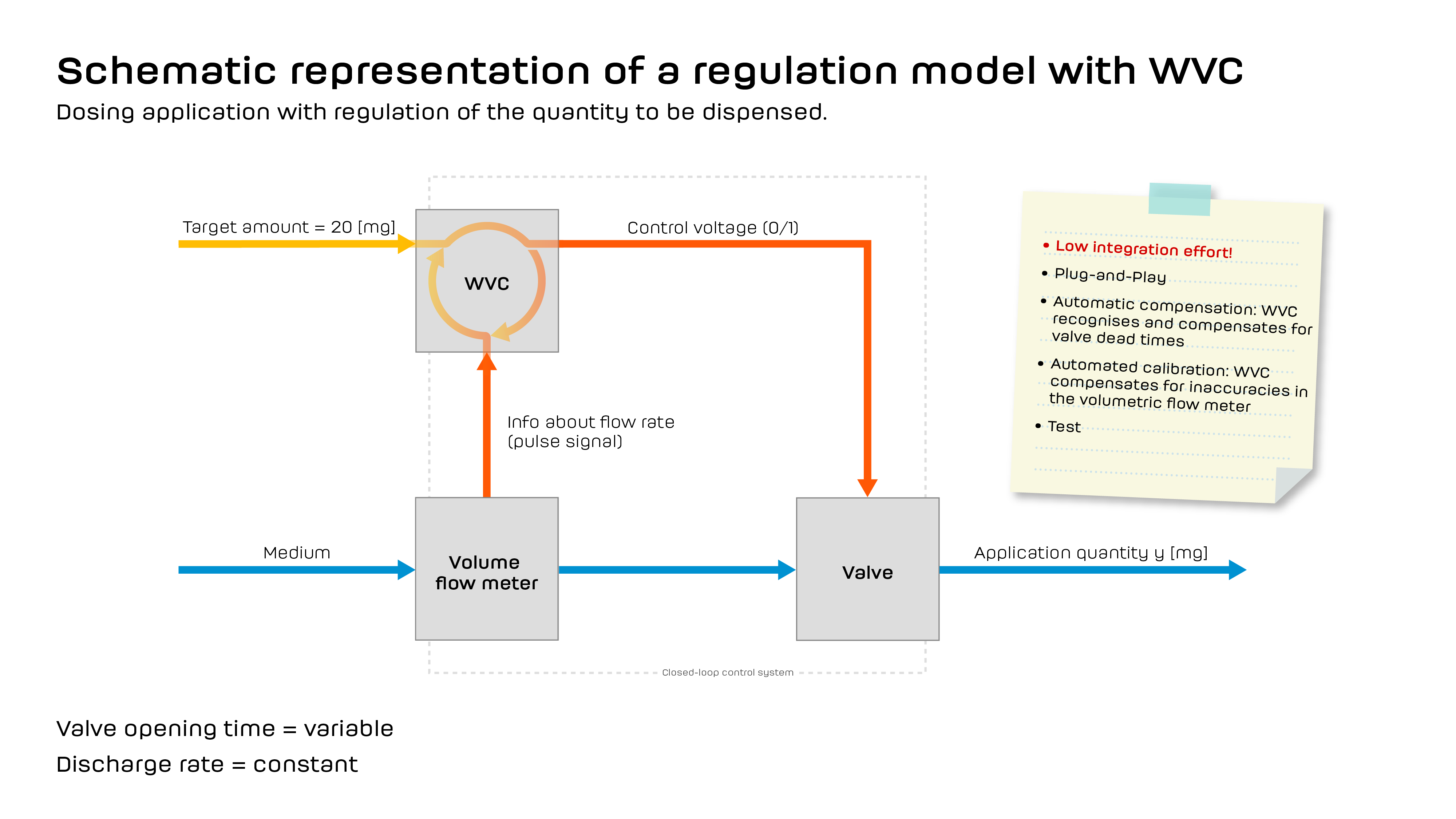
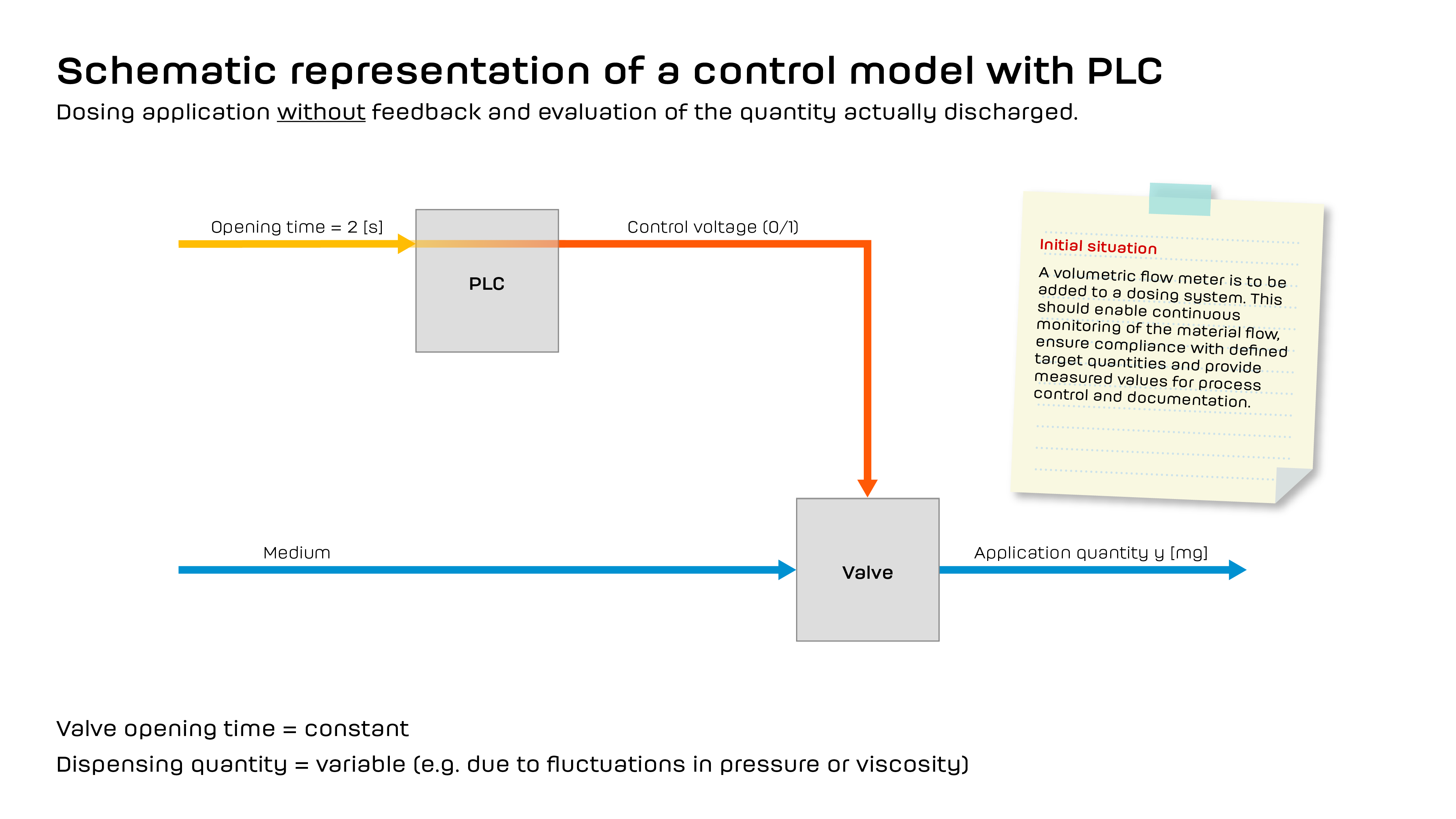
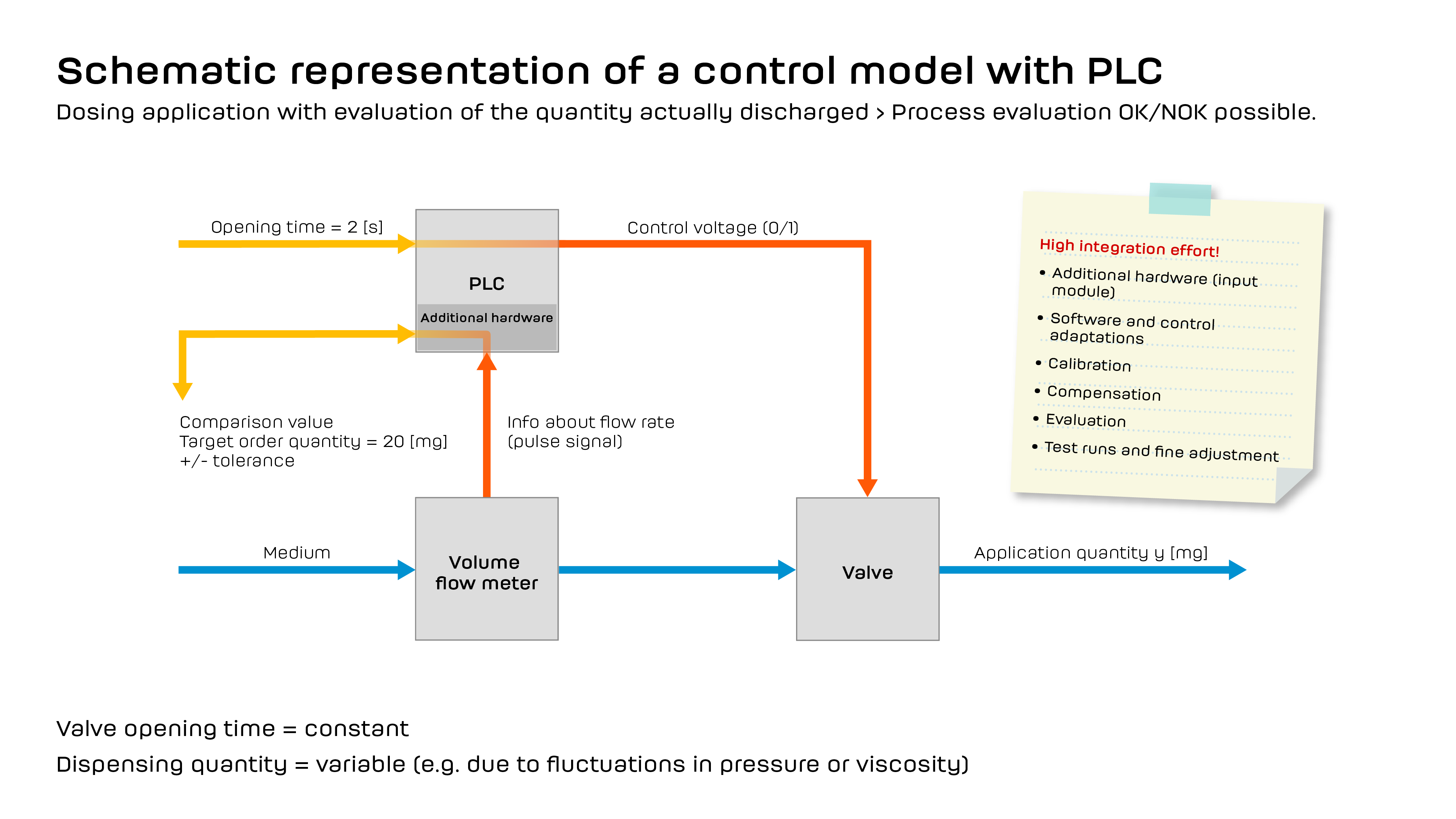
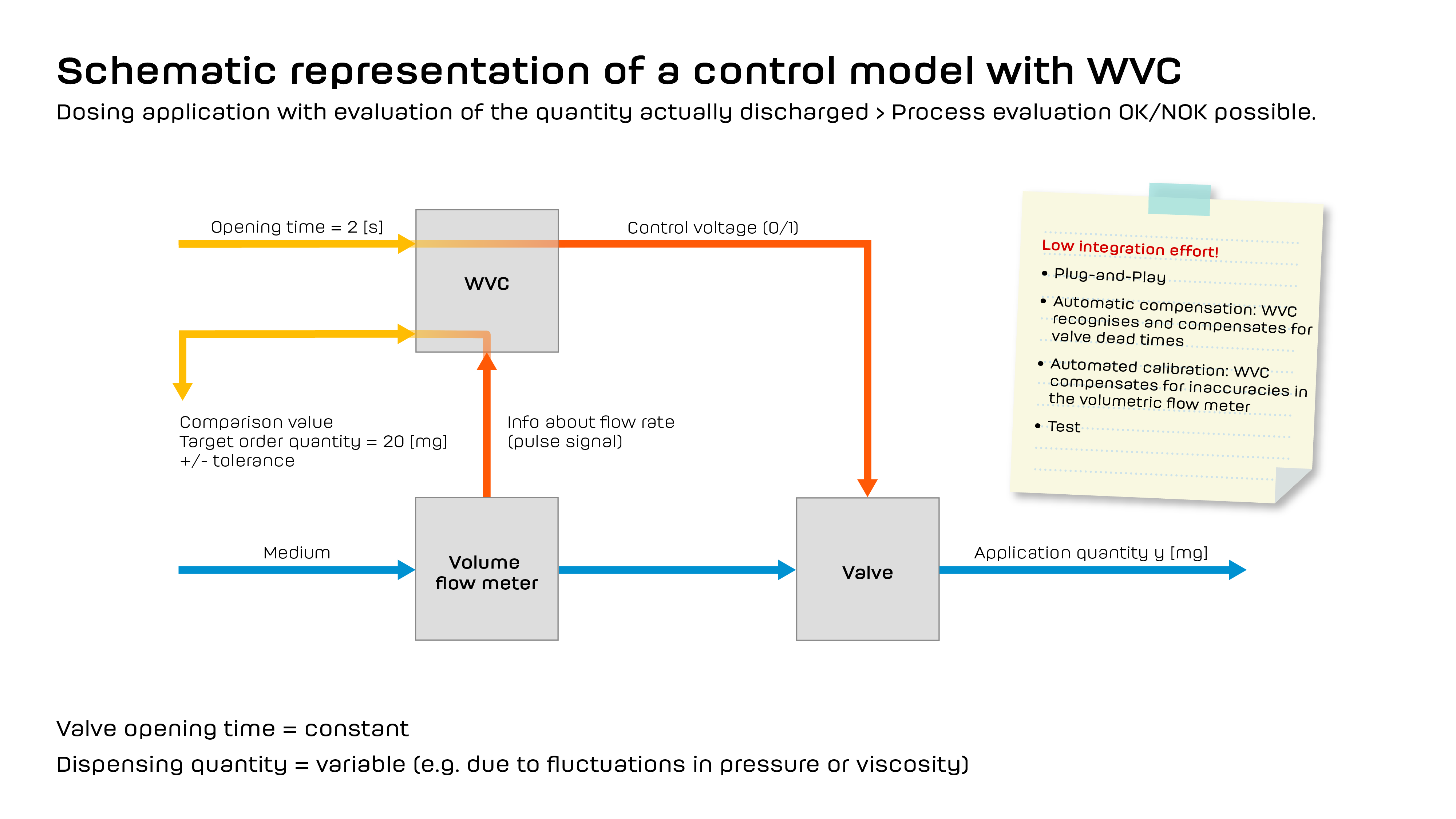
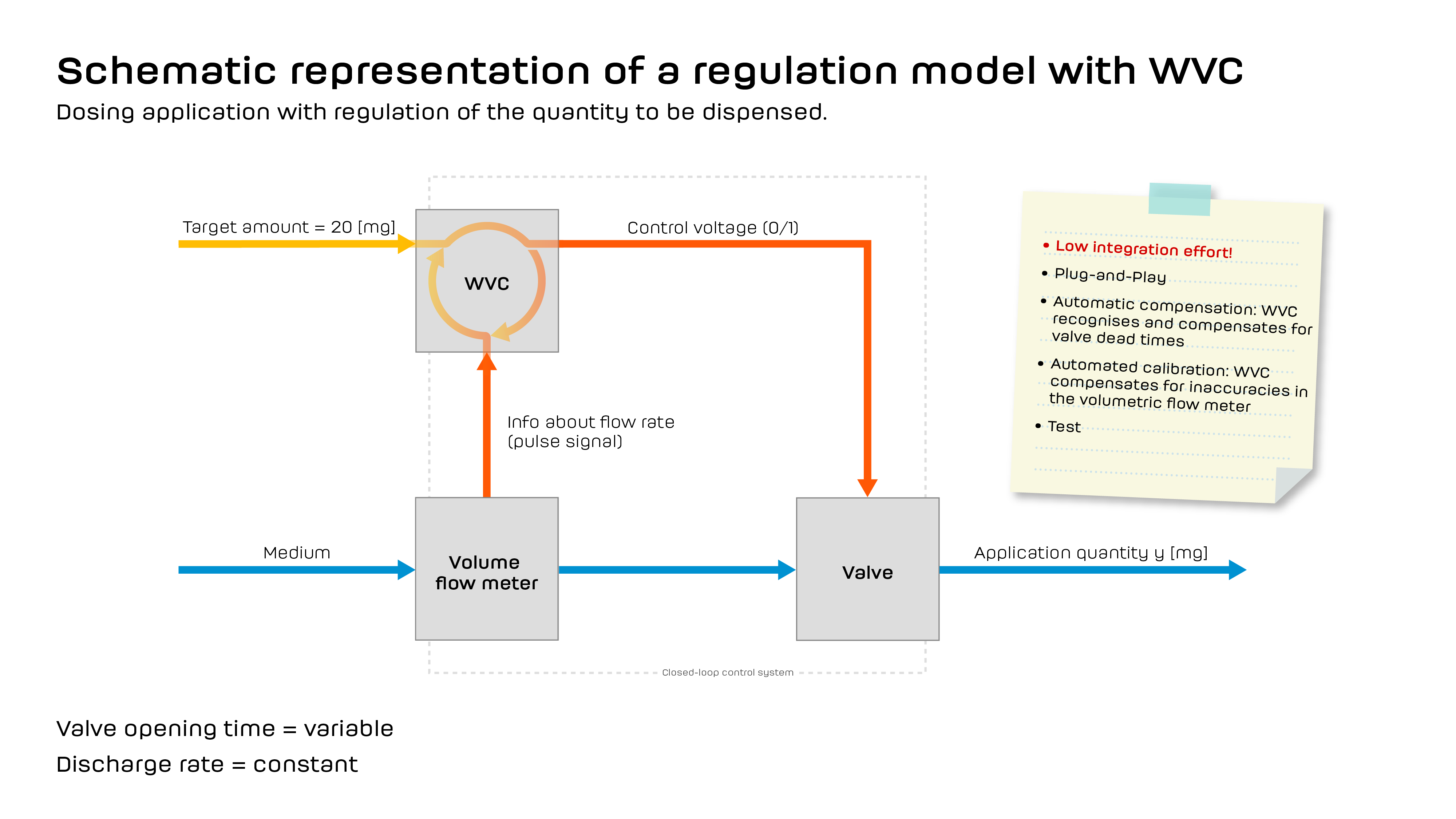
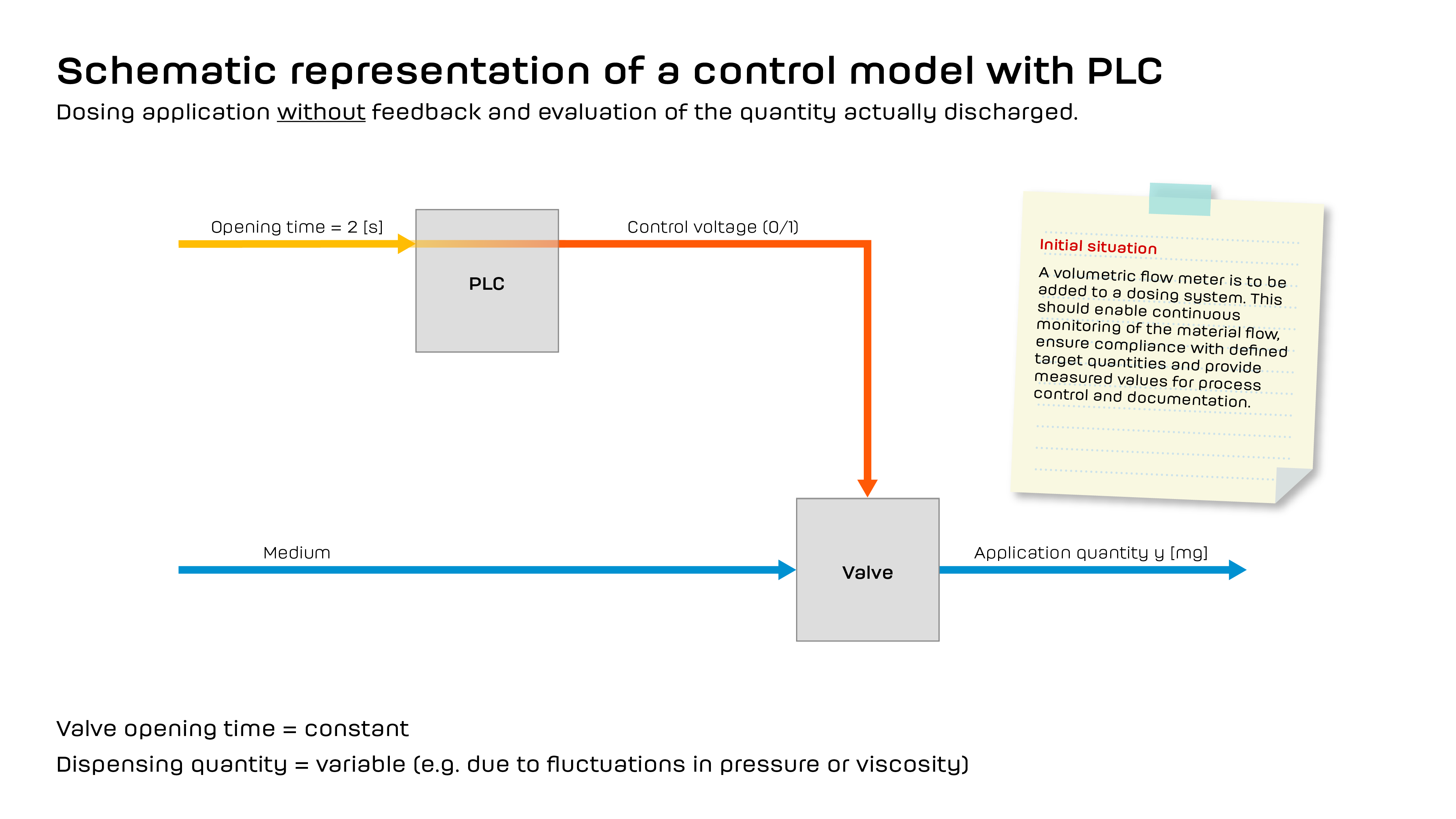
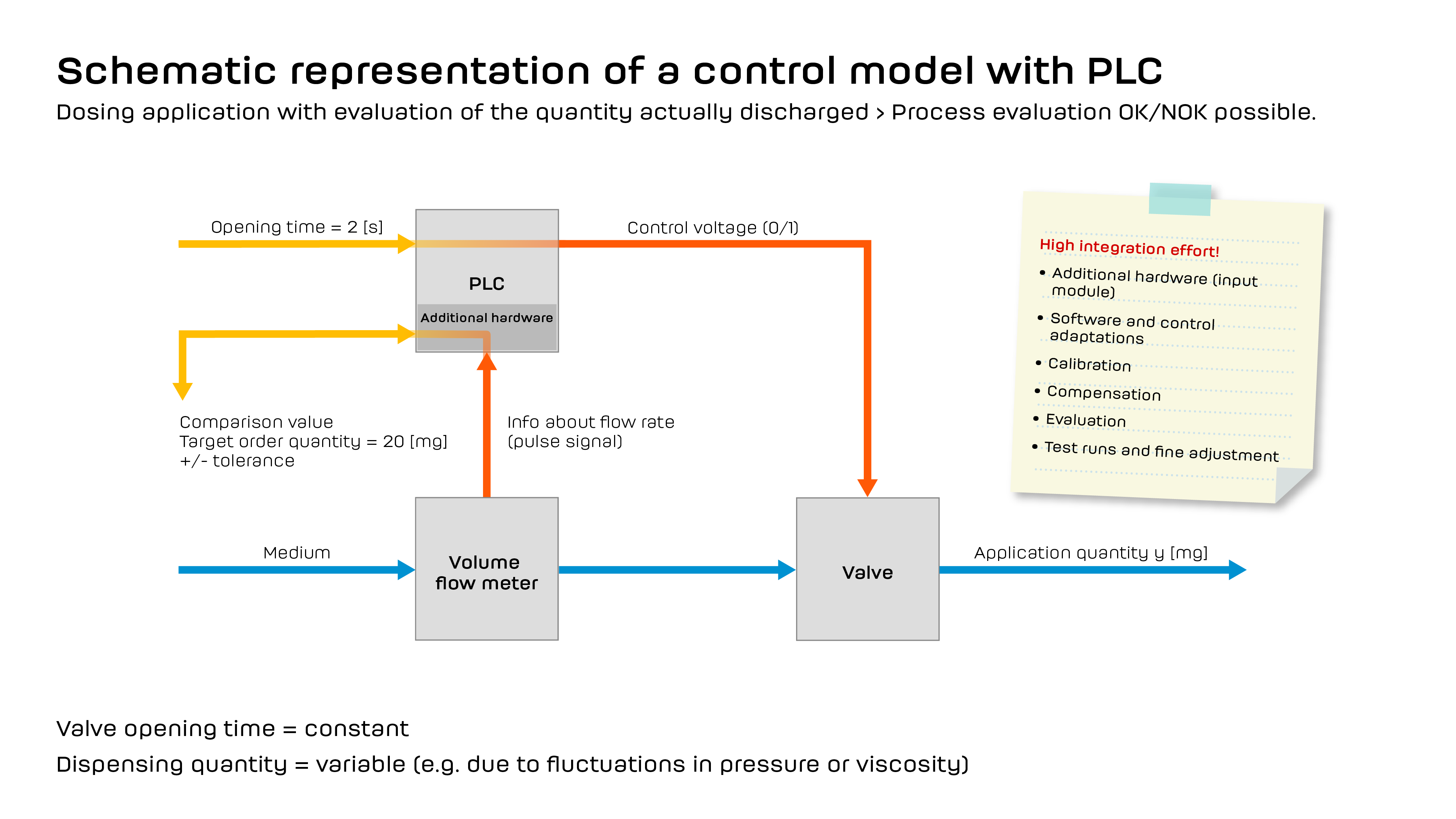
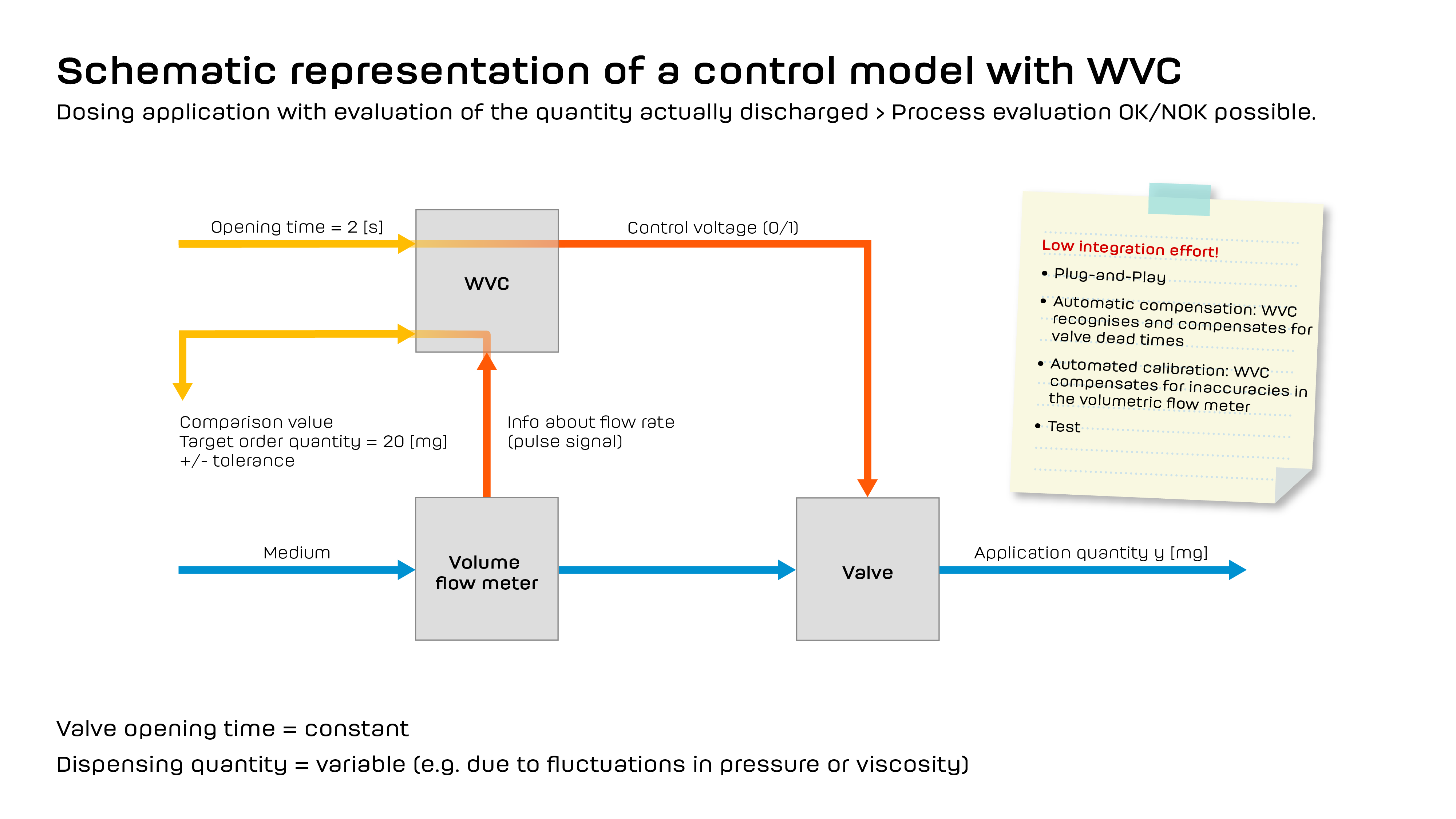
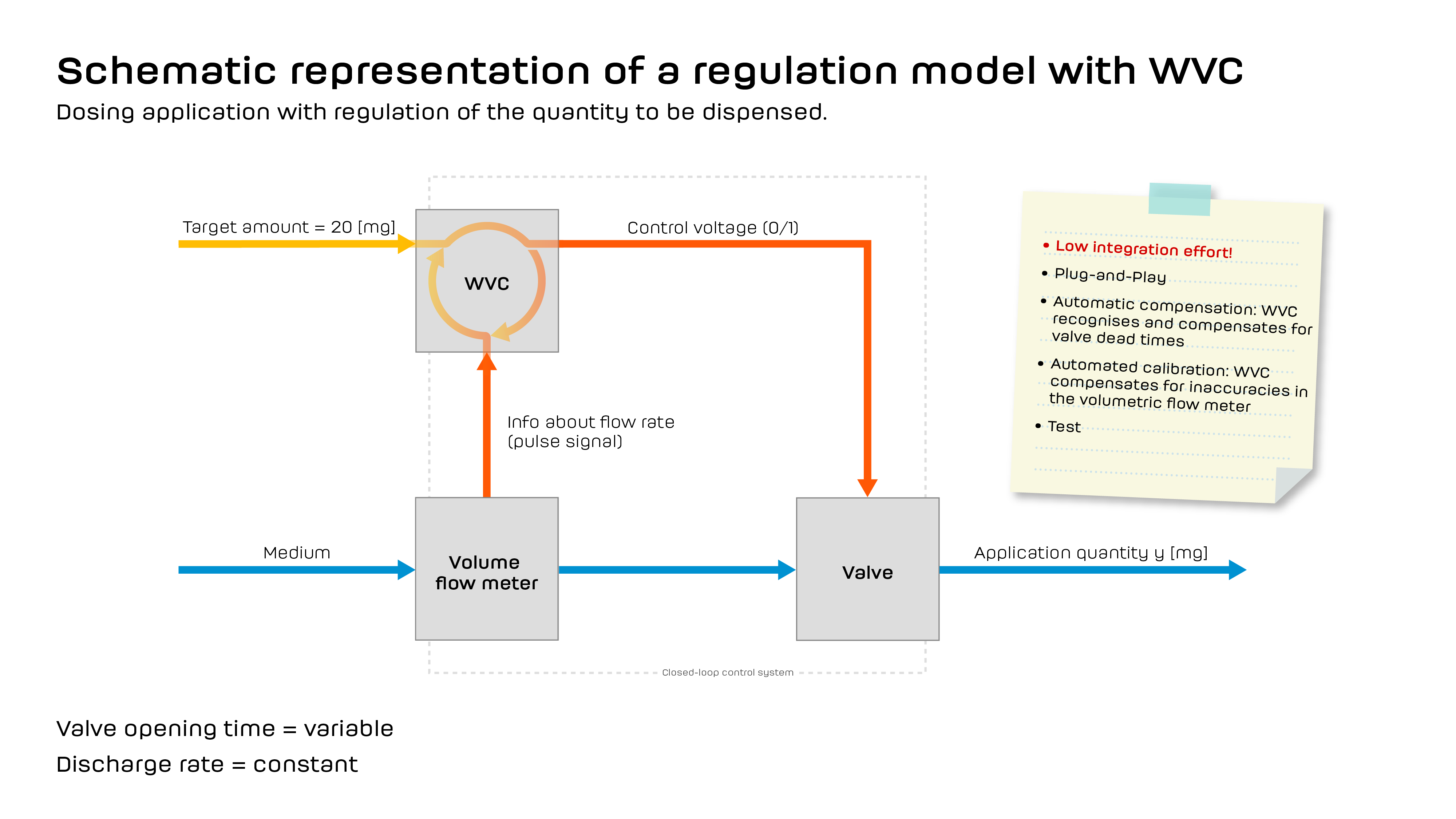
27 Feb 2025, 11:00:00
In industrial dosing processes, controlling the quantity dispensed is crucial for quality and efficiency. But how can you ensure that dosing is always precise? We compare four different control models and show how the Walther Valve Controller (WVC) drastically reduces the integration effort.
Figure 1 (🇬🇧 5): Classic PLC control without feedback The valve is opened for a fixed time ⏱️, but the actual quantity discharged can fluctuate - e.g. due to changes in pressure or viscosity. Without measuring the actual discharge quantity, process reliability remains limited.
Figure 2 (🇬🇧 6): PLC with volume flow meter for process evaluation (IO/NIO) Measuring the discharged quantity is possible, but involves a high level of integration effort (additional hardware, software adaptations, calibration and fine adjustment).
Figure 3 (🇬🇧 7): WVC control with volume flow meter for process evaluation (IO/NIO) Low integration effort via plug-and-play: Automatic calibration and compensation of dead times facilitate commissioning. The volumetric flow is controlled directly via the WVC, without complex PLC adaptations.
Figure 4 (🇬🇧 8): WVC as a control system The highest level of process control: regulation instead of control! The WVC dynamically adjusts the valve opening time to ensure a constant discharge rate - regardless of external influencing factors such as pressure or viscosity fluctuations.
Conclusion: If you want process reliability with minimum effort, there is no way around a solution with the WVC!
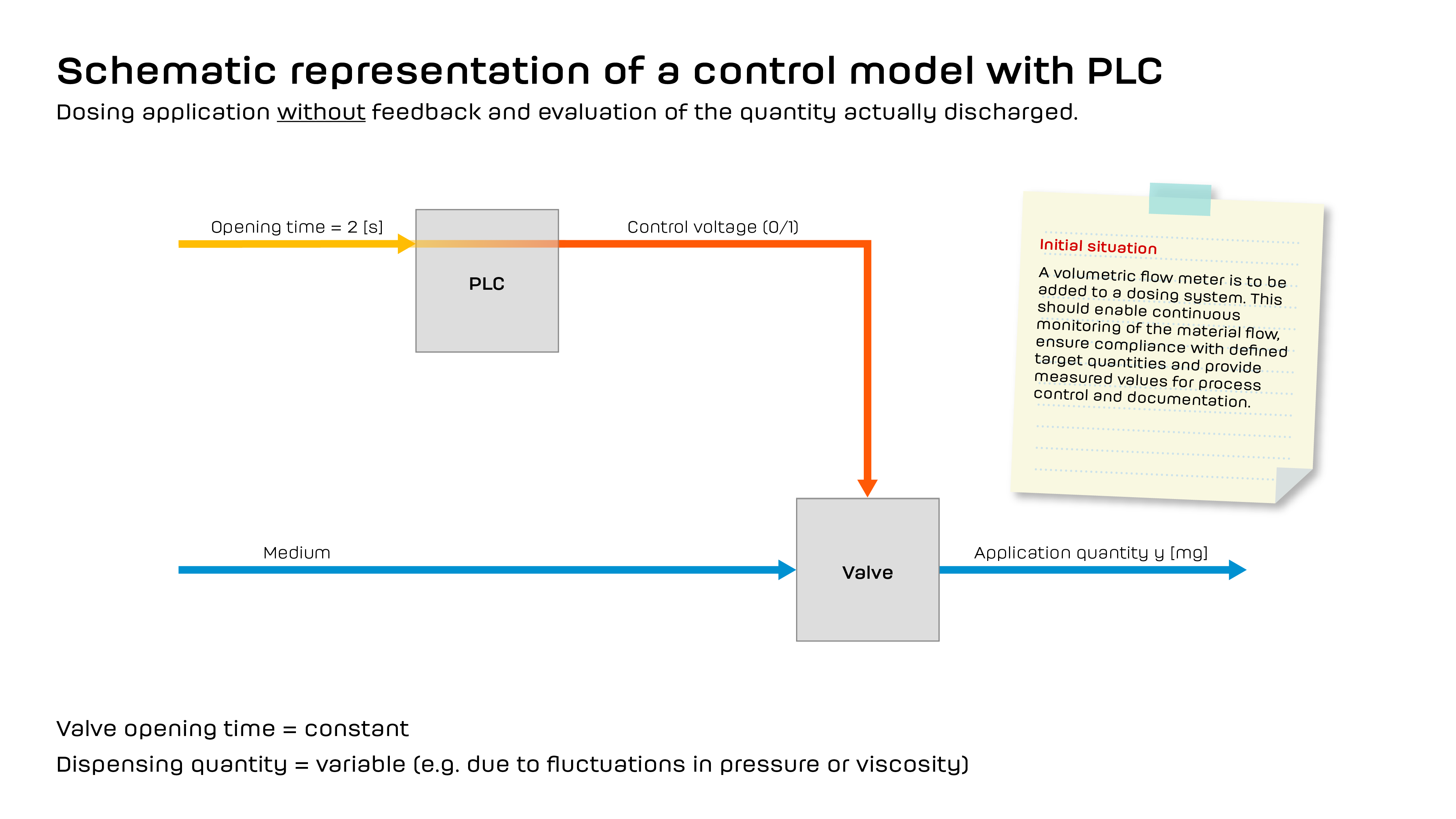
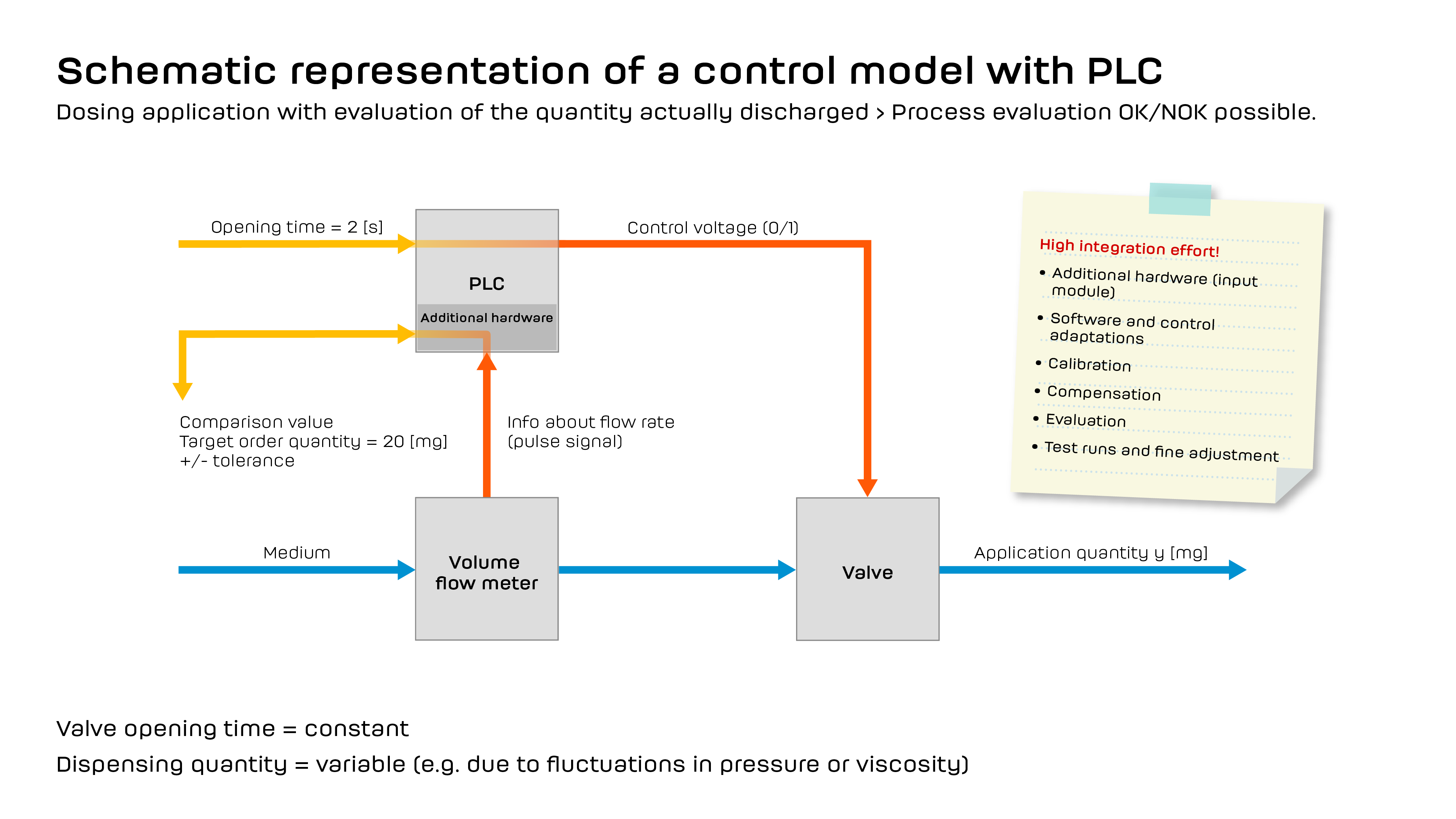
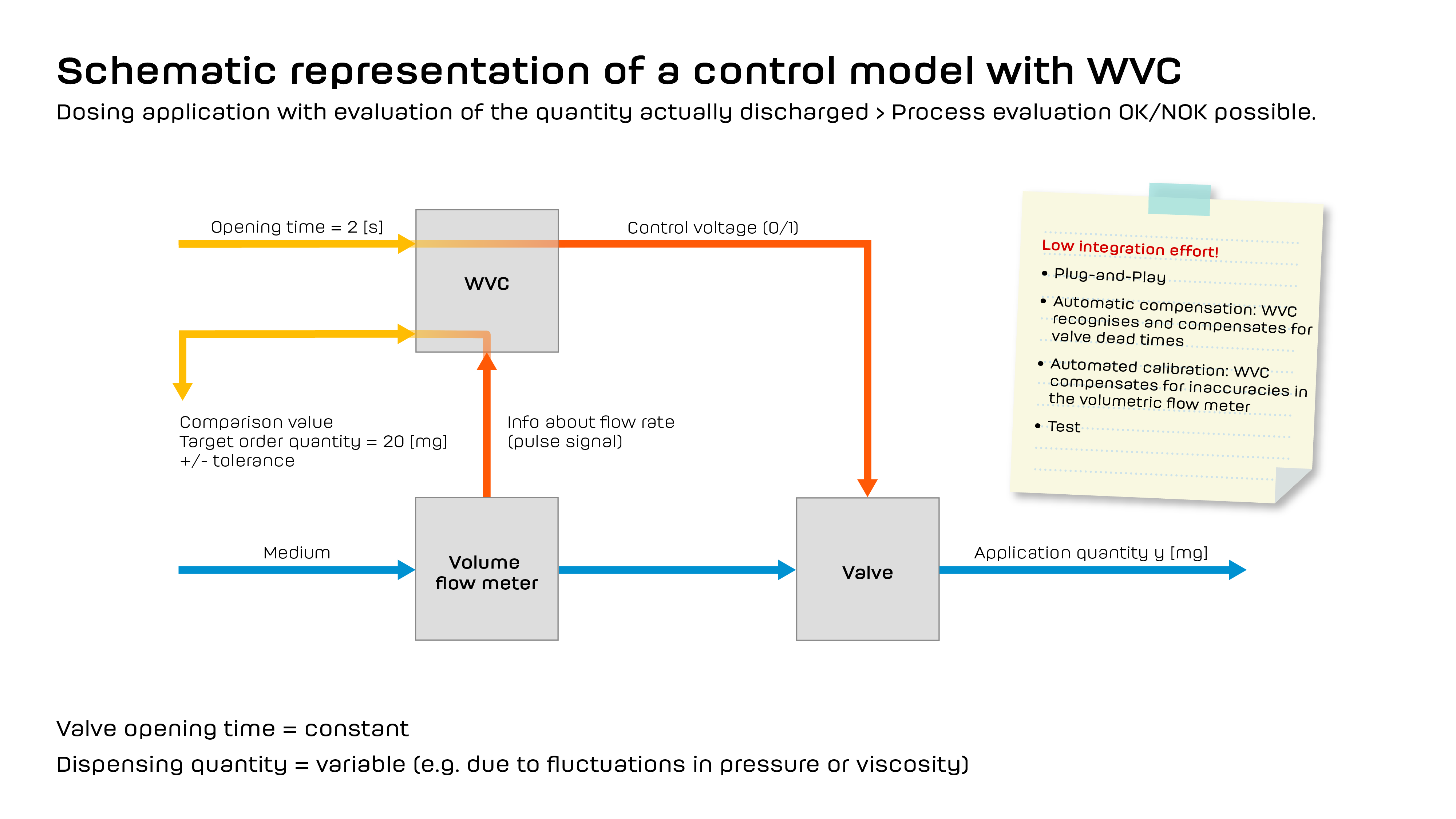
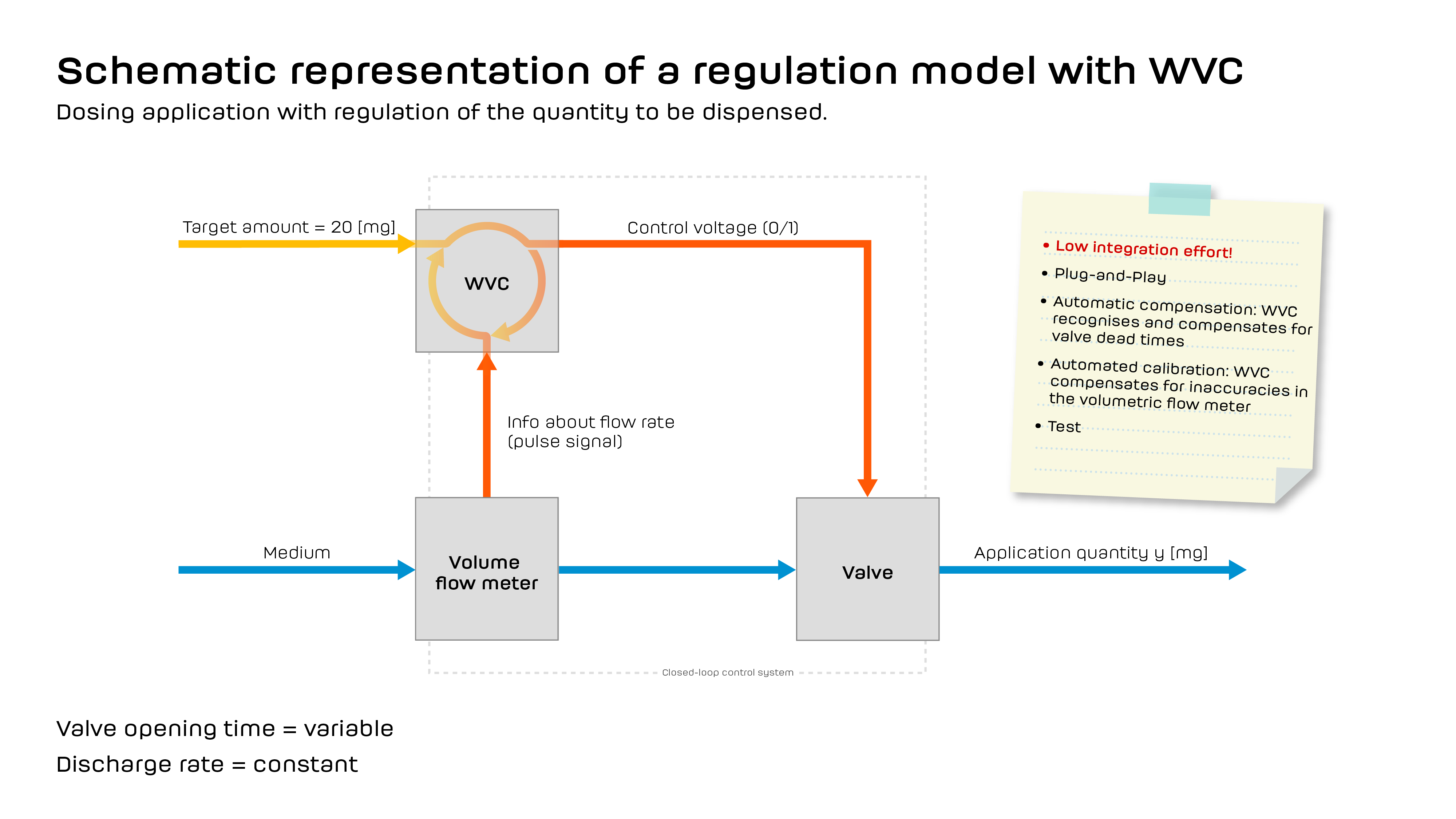
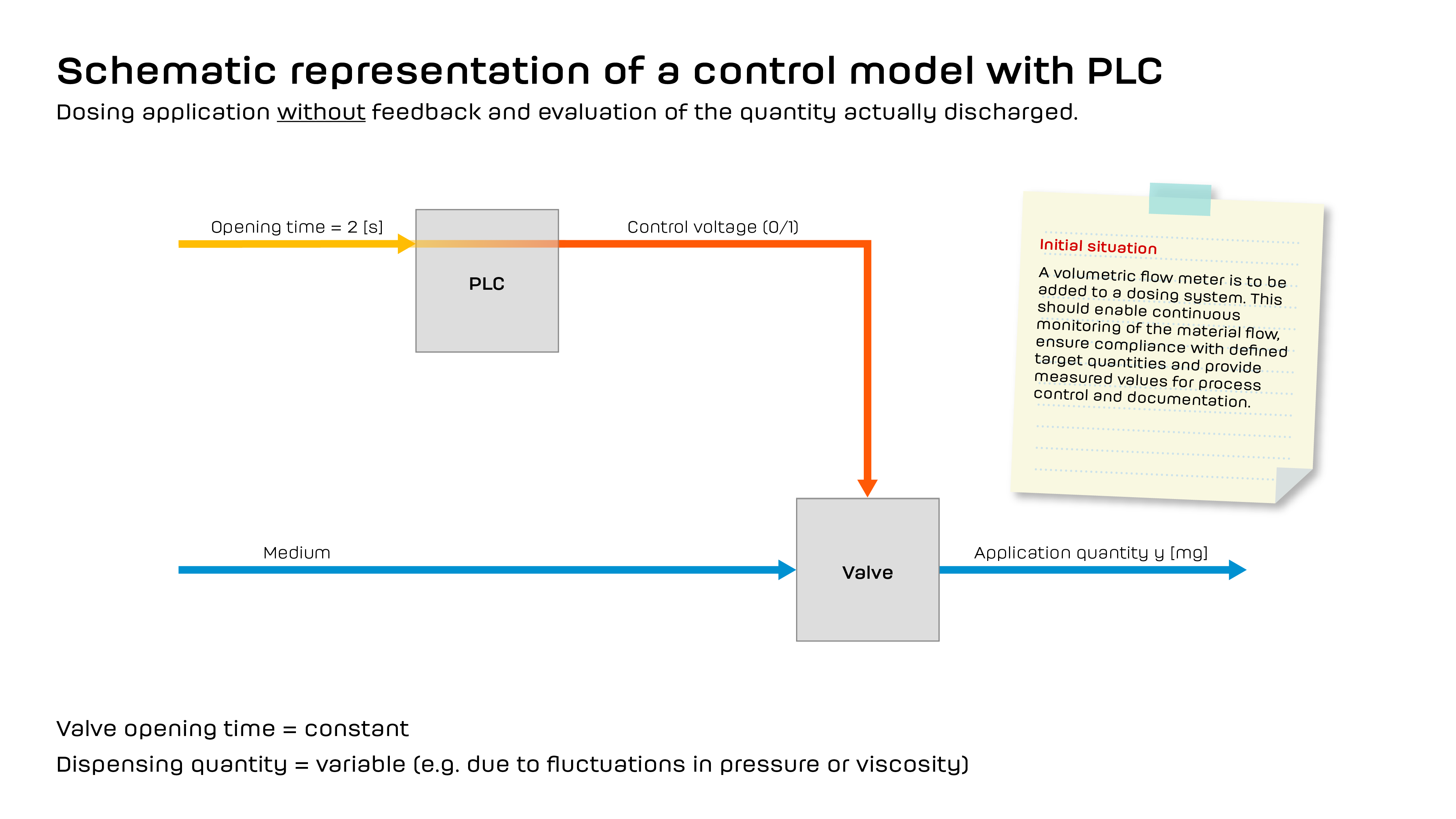
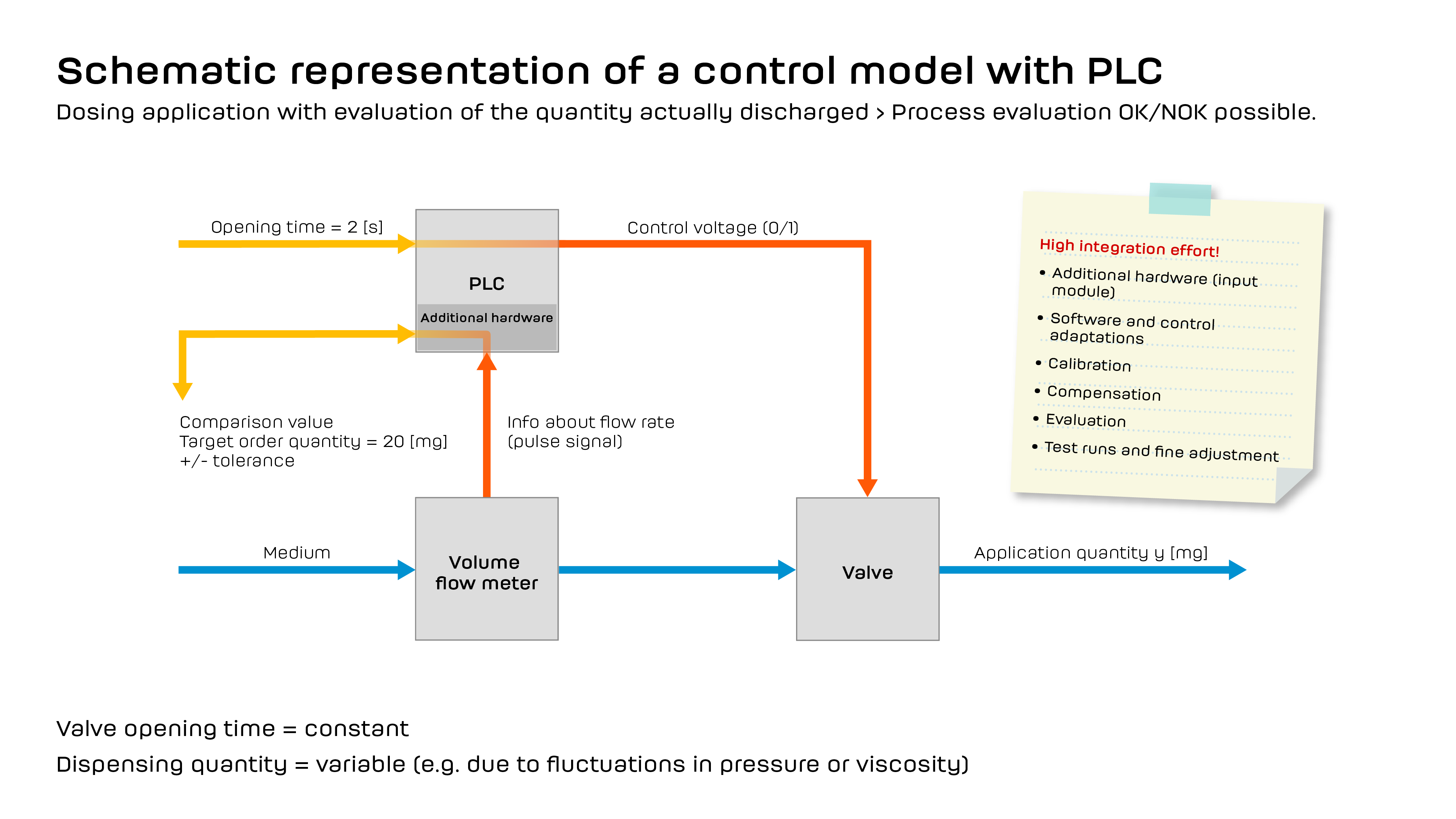
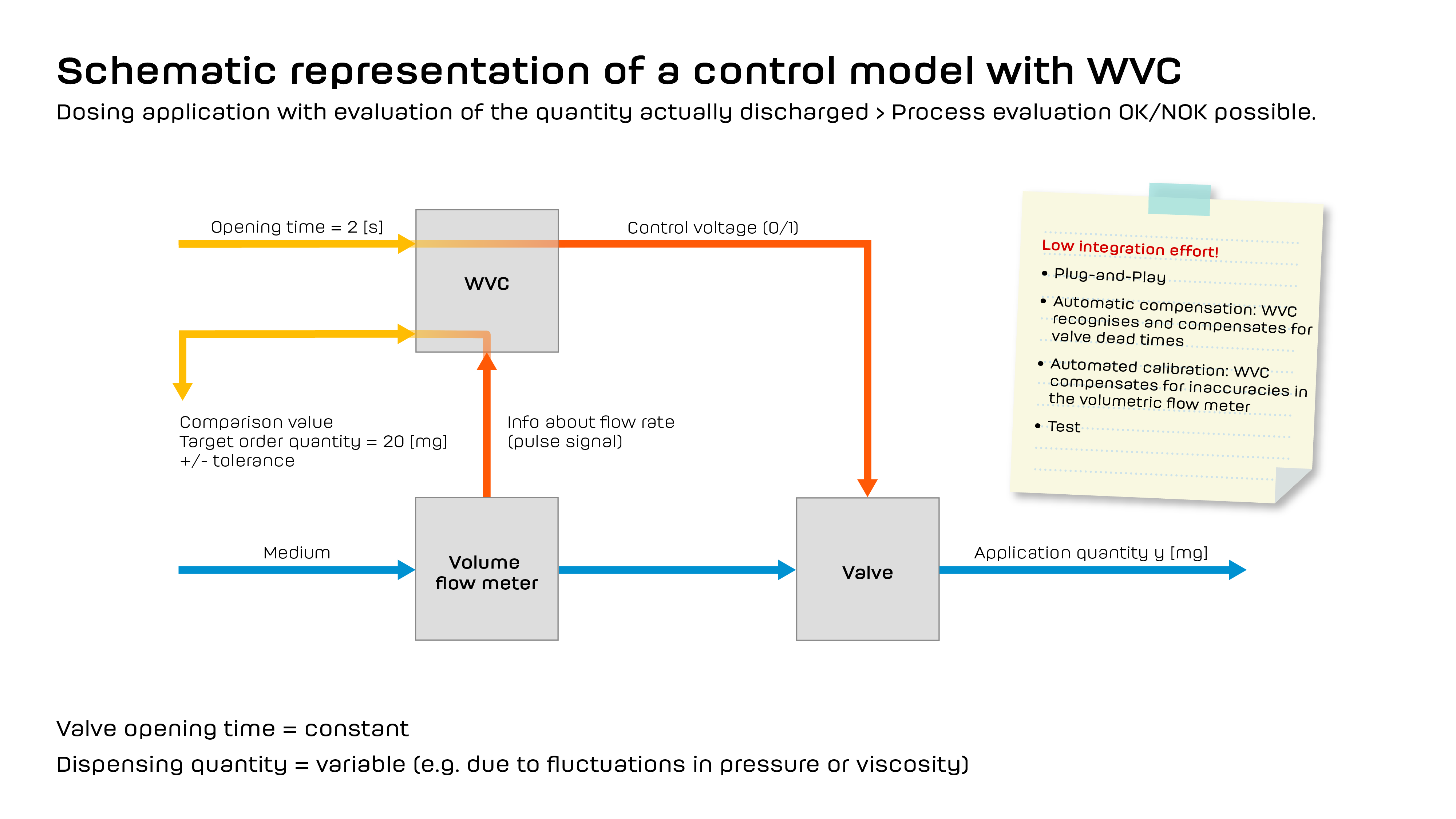
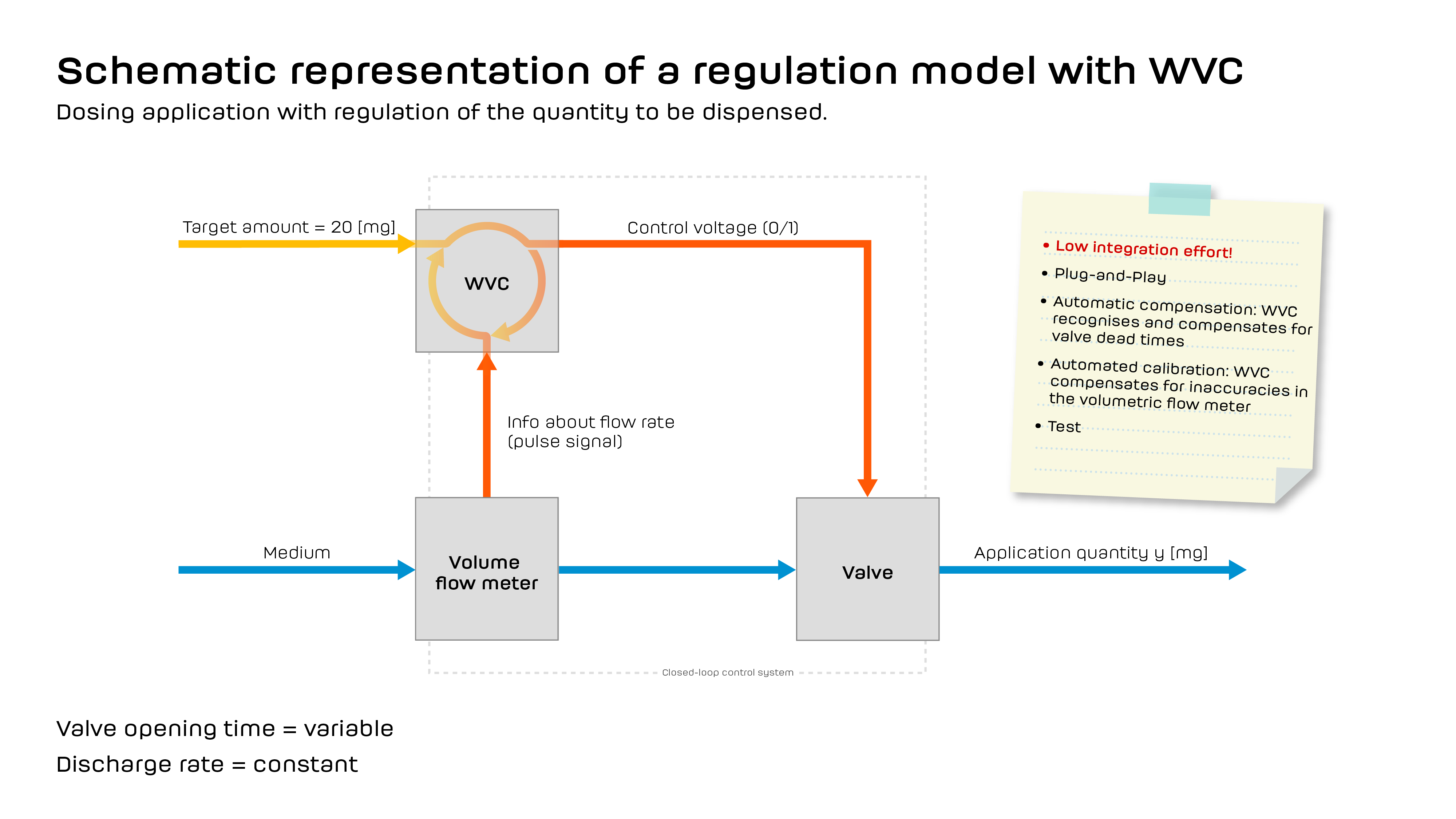
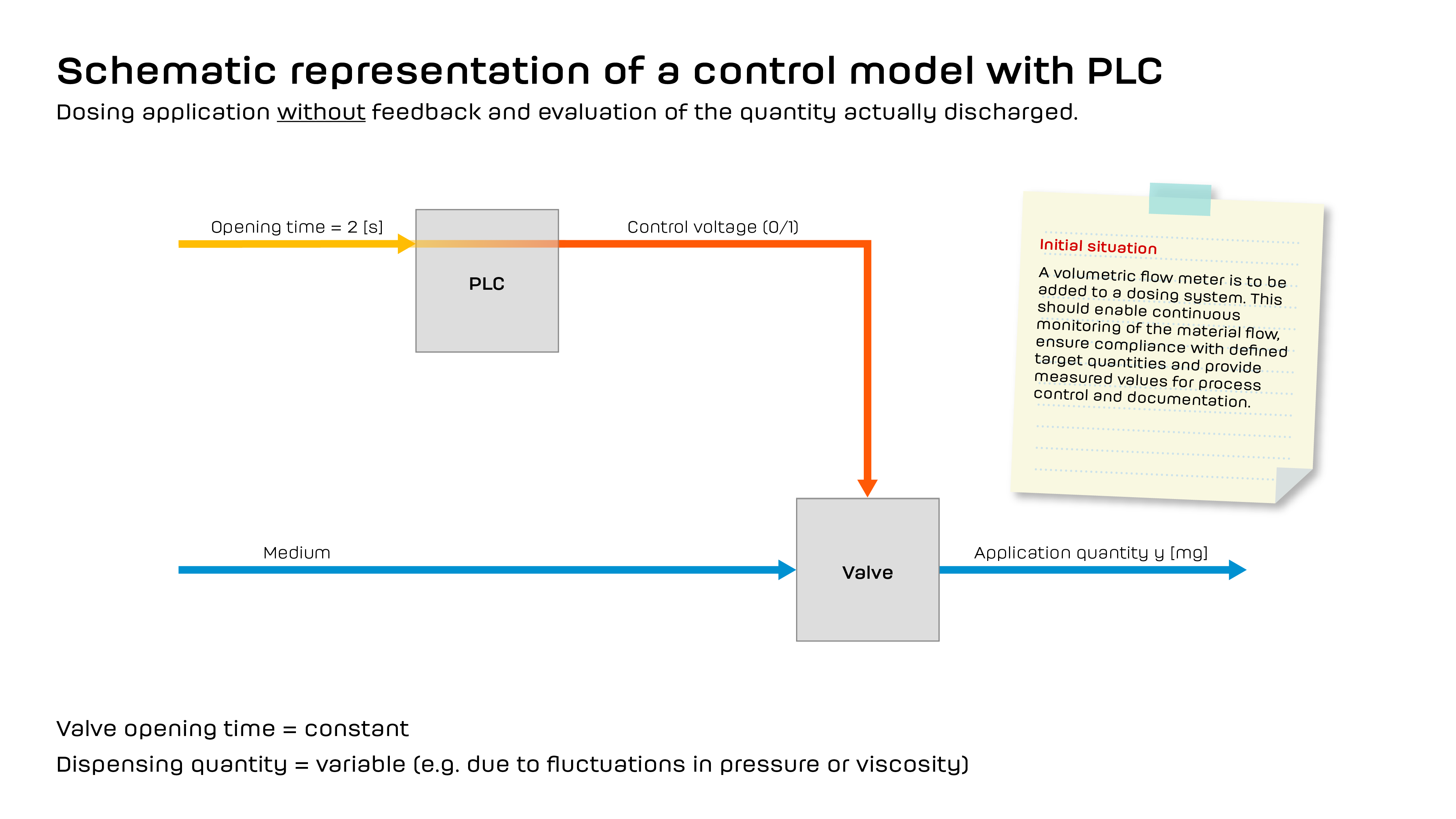
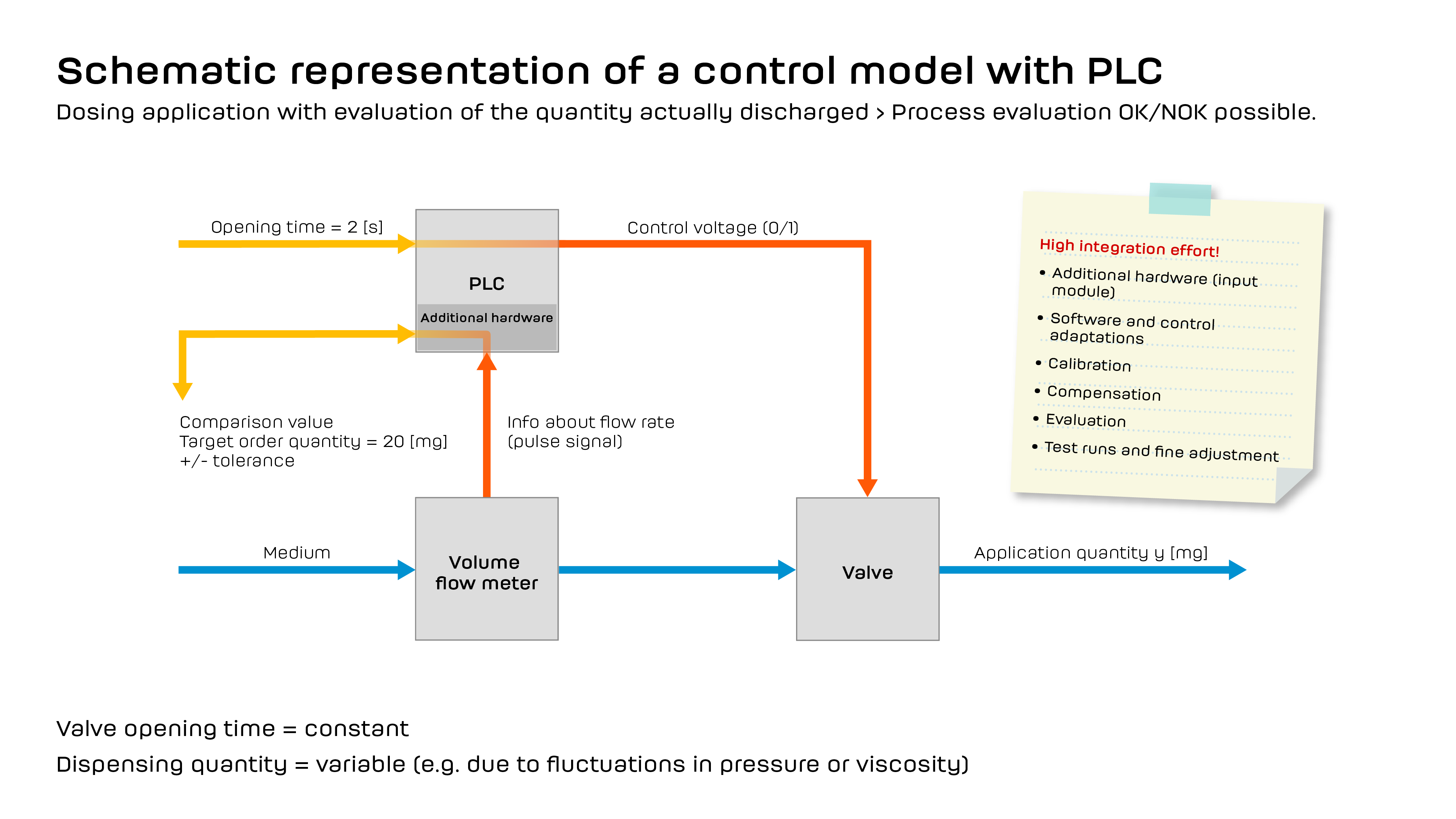
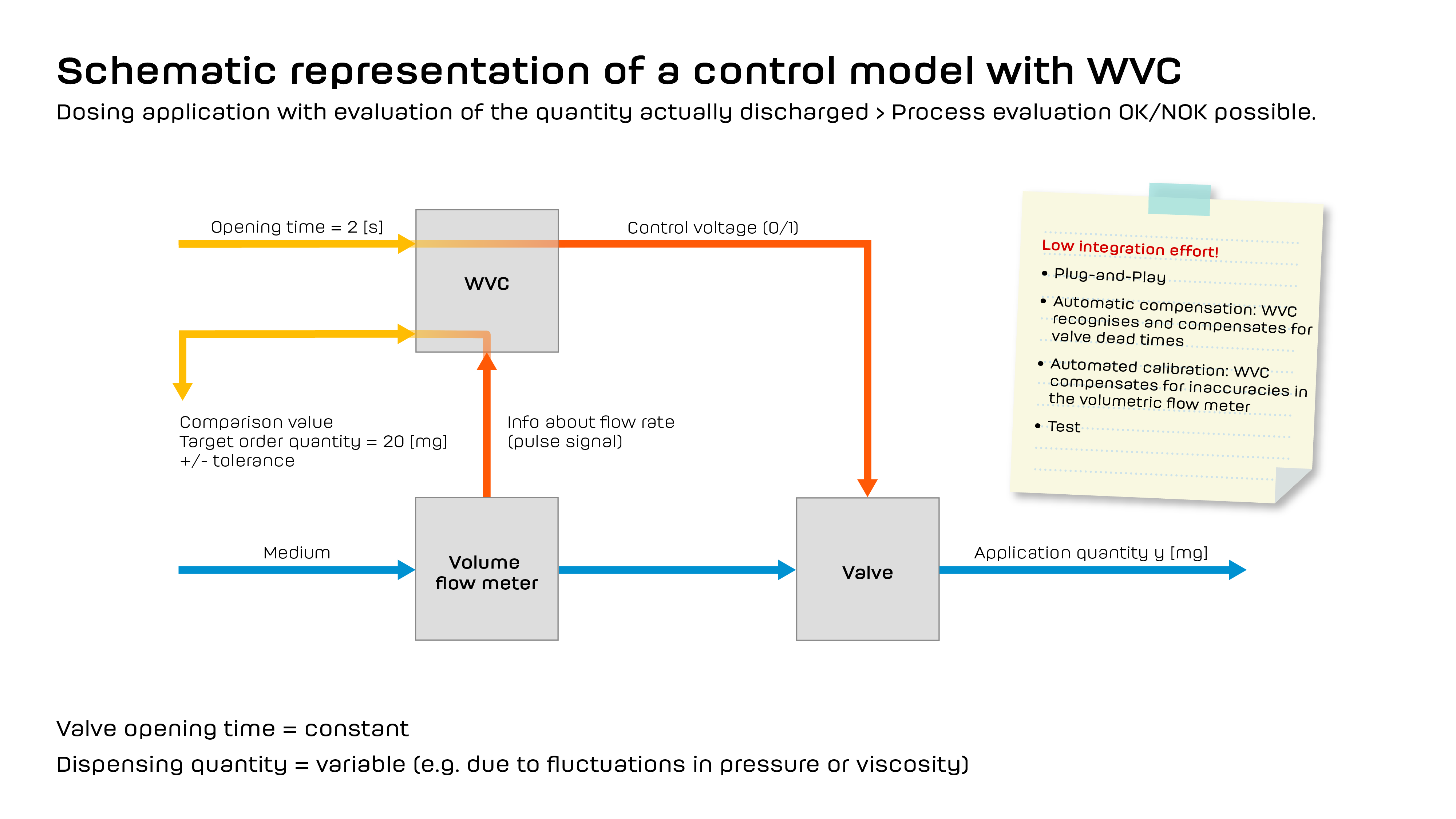
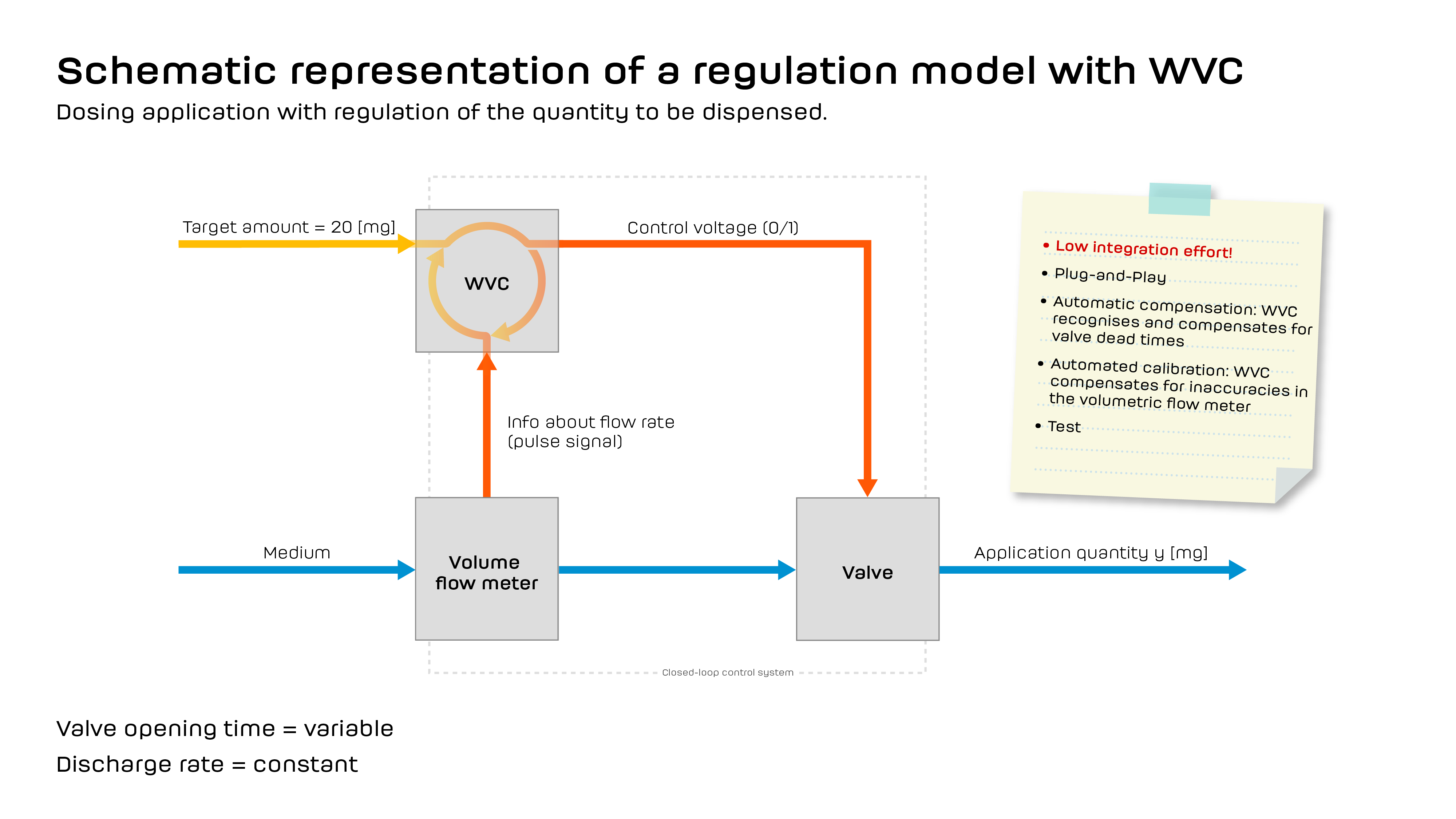
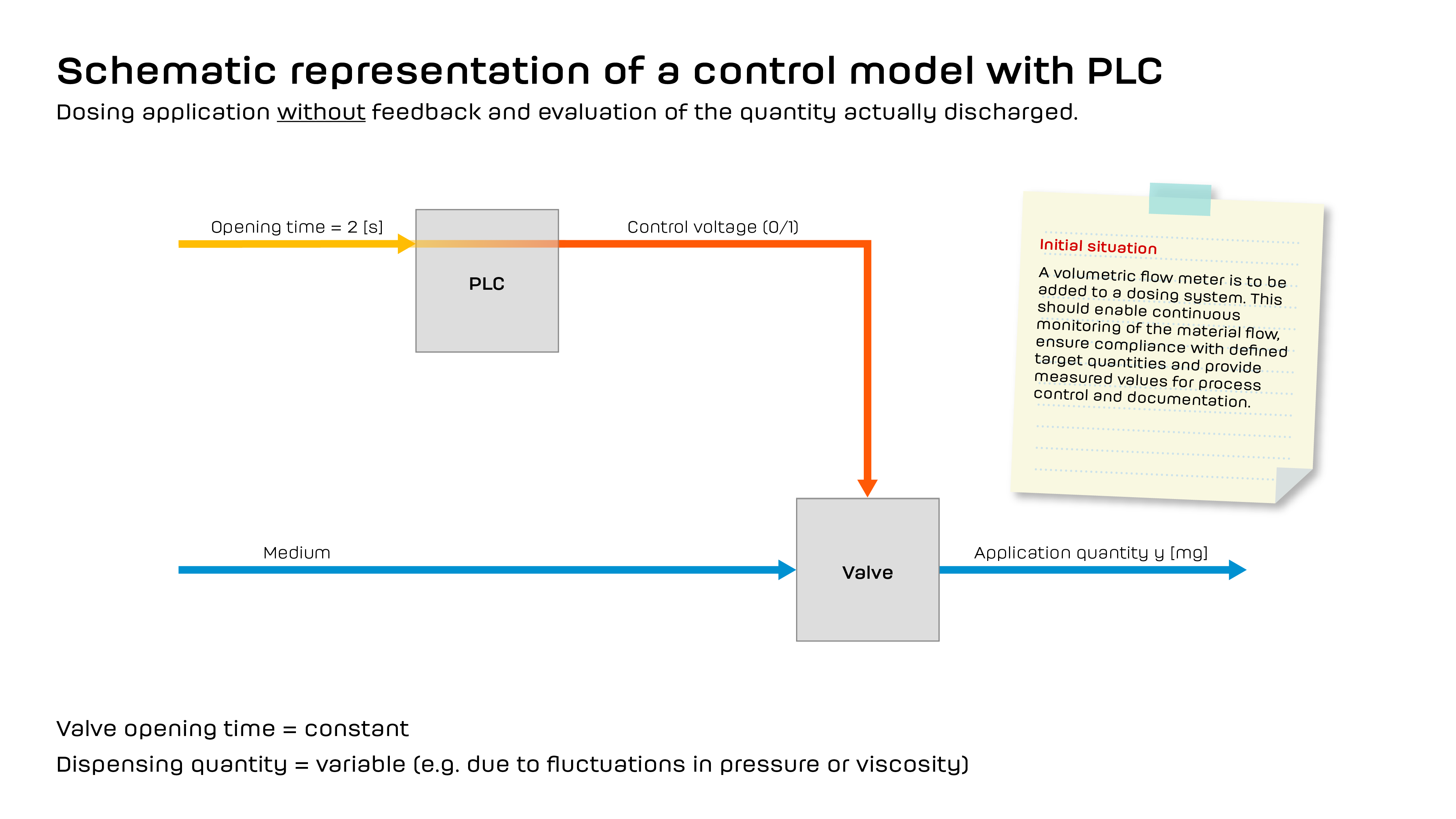
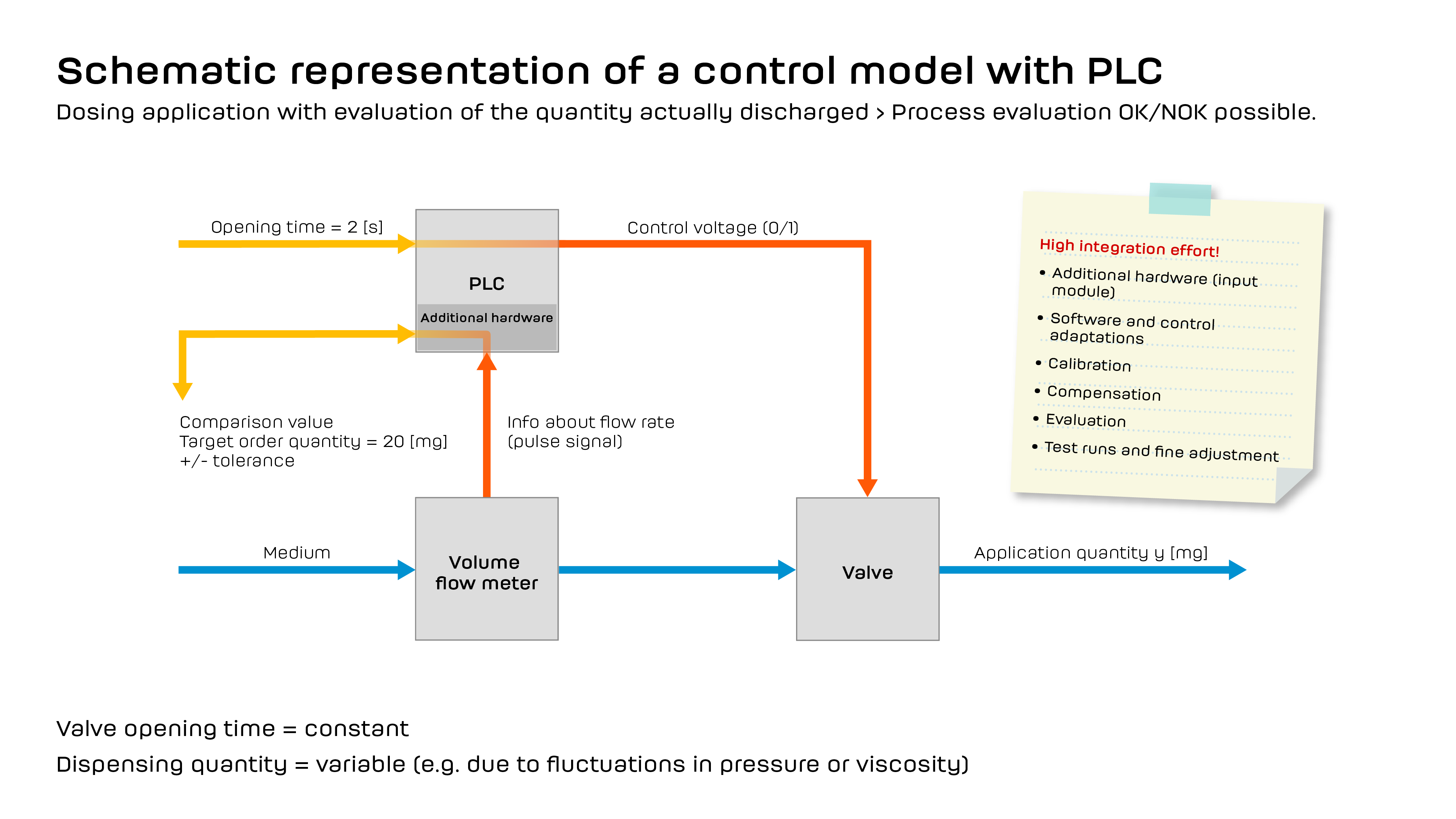
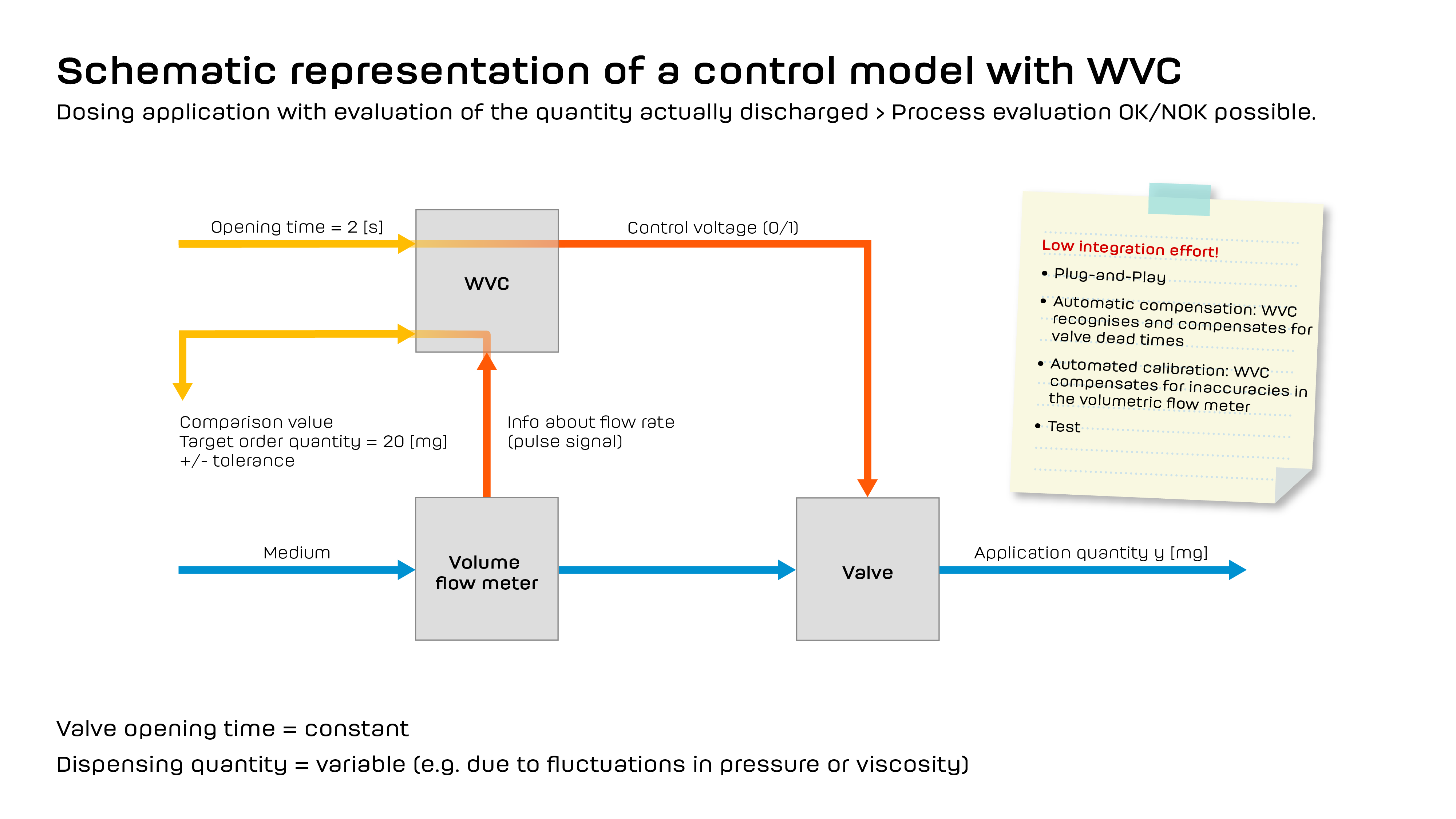
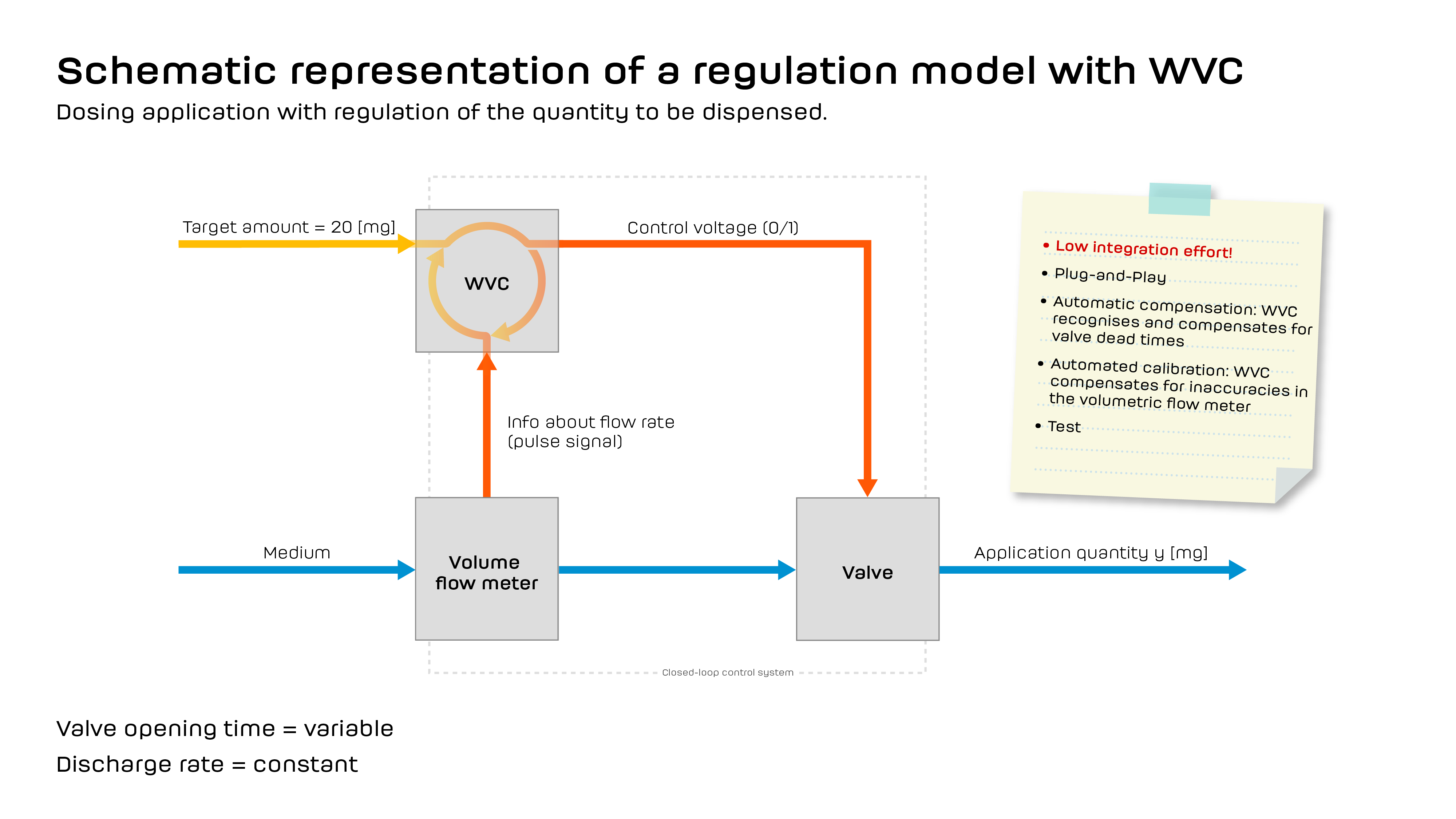
Efficient dosing processes: Control vs. regulation - what makes the difference?
In industrial dosing processes, controlling the quantity dispensed is crucial for quality and efficiency. But how can you ensure that dosing is always precise? We compare four different control models and show how the Walther Valve Controller (WVC) drastically reduces the integration effort.
Figure 1 (🇬🇧 5): Classic PLC control without feedback The valve is opened for a fixed time ⏱️, but the actual quantity discharged can fluctuate - e.g. due to changes in pressure or viscosity. Without measuring the actual discharge quantity, process reliability remains limited.
Figure 2 (🇬🇧 6): PLC with volume flow meter for process evaluation (IO/NIO) Measuring the discharged quantity is possible, but involves a high level of integration effort (additional hardware, software adaptations, calibration and fine adjustment).
Figure 3 (🇬🇧 7): WVC control with volume flow meter for process evaluation (IO/NIO) Low integration effort via plug-and-play: Automatic calibration and compensation of dead times facilitate commissioning. The volumetric flow is controlled directly via the WVC, without complex PLC adaptations.
Figure 4 (🇬🇧 8): WVC as a control system The highest level of process control: regulation instead of control! The WVC dynamically adjusts the valve opening time to ensure a constant discharge rate - regardless of external influencing factors such as pressure or viscosity fluctuations.
Conclusion: If you want process reliability with minimum effort, there is no way around a solution with the WVC!
Weitere Beiträge
Price on request
Price on request
Price on request
Price on request
Price on request
Price on request
Price on request
Price on request
Price on request
Price on request
Price on request
Price on request
Price on request
Price on request
Price on request
Price on request
Price on request
Price on request
Price on request
Price on request
Price on request
Price on request
Price on request
Price on request